「生産性ロードマップ戦略」—儲かる工場経営を目指して—第305話 現場の生産能力を計算できないのには理由がある
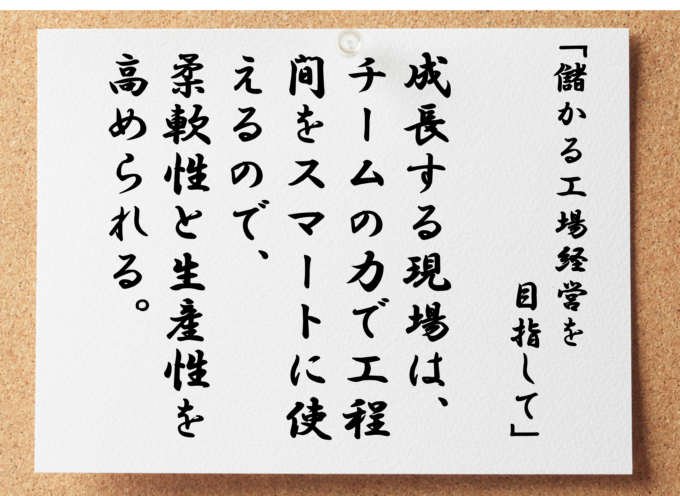
「どこまでできるかよくわかりません。」
自社工場の生産能力について語った部品メーカー、幹部の言葉です。
先日の個別相談では工数計画の現状から話が始まりました。ベテラン従業員の意見に基づいて工場の生産能力を評価しています。ただし、明確な計算根拠はありません。
現場が忙しくなるたびに受注可否判断ですったもんだしている現場です。結局、本当の生産能力は把握されていません。冒頭の言葉です。
工数計画では能力と負荷を比べます。負荷を計算し「わが社の能力」と比較するのです。そうして受注可否判断します。
能力>負荷
能力=負荷
能力<負荷
判断基準は「わが社の能力」です。負荷との大小関係でどう対応するかルールを決めておく必要があります。
貴社は生産能力が明らかになっていますか?
生産能力の基本式はあります。しかし、その式に当てはめればすぐに計算できるほど現場は単純ではありません。
生産能力は生産形態にも影響を受けます。特に設備レイアウトです。設備レイアウトは2通りに分類されます。
機能別レイアウト
製品別レイアウト
機能別レイアウトでは、「切削」「プレス」「曲げ」等々の工程(機能)毎に設備を集約して並べます。一方、製品別レイアウトでは、特定の製品だけを流せるように設備を並べます。コンベアーで繋がった一貫ラインのイメージです。
機能別レイアウト、製品別レイアウト、それぞれに目的があります。
製品別レイアウトの狙いは生産性です。特定の製品を流すためのレイアウトですから効率が高まります。製造すれば製造するほどにコストが下がるのです。逆に言うと、生産量が多くないとその効果を発揮できません。
製品Aだけ、製品Bだけ、製品Cだけのための設備レイアウトです。ムダもあります。受注が製品Aに偏ると、製品B、製品Cの設備の稼働は減るからです。規模の経済で儲けを積みあげる大手の戦略と言えます。
製品別レイアウトの能力計算は簡単です。そもそも特定の製品、製品群を専門に製造するレイアウトにしたのは、一定水準の生産能力が欲しいからです。
能力計算ができない製品別レイアウトは原則、あり得ません。専門性が高いので各種生産指標も特定し易くなっています。
機能別レイアウトの狙いは柔軟性です。工場には工程(機能)毎のエリアがあります。製品は仕様に応じて、必要なエリアを渡り歩けばいいわけです。同じ工程を行ったり来たりすることも、特定の工程をスキップすることも簡単にできます。
この柔軟性が製品別レイアウトの特徴です。多品種少量生産に向いています。
中小製造企業の多くは下請け型モデルです。QCDの決定権を親企業に握られているので、現場の柔軟性を高めておく必要があります。特急や突発、変更の要望も少なくありません。
そうした要望に応えるのが機能別レイアウトです。
中小現場では必然的に機能別レイアウトが多くなります。ただ、柔軟性が高い故に、製品別レイアウトとは異なり、各種生産指標の設定は、少々面倒です。
先の幹部の現場も機能別レイアウトなので、多くの中小現場と同じく、生産能力を把握するのに苦労しています。
機能別レイアウトは「工程間」の存在がキモです。工程間のお陰で柔軟性が高まる一方、工程間が無駄の原因にもなります。時間的な無駄の原因です。
機能別レイアウトの工程間連携は原則、属人的になります。この属人的がイイ方向へ働く場合と悪い方向へ働く場合があるのです。現場のベクトル揃え次第です。
現場のベクトルが揃っていて、チームの力で仕事ができていれば、高度な連携により、柔軟性とリードタイム短縮の両立が可能となります。
その一方で、現場のベクトルが揃っていなくて、チームではなく、個の力でしか仕事ができていなければ、「工程間」は時間的ロスの原因になってしまいます。
工程間でモノが停滞するのです。属人的が悪い方向へ働くと一気通貫で流そうとする視点が抜けます。
自分の分担だけやっていればいいだろうと考える作業者がいると、機能別レイアウトはその良さを発揮できなくなるのです。属人的なボトルネックが存在する現場と言えます。
先の幹部の現場でもベテラン従業員がボトルネックになっているとのこと。そうであるなら、その解消から考えなければなりません。
機能別レイアウトでは「工程間」の存在がキモです。柔軟性を高めながらリードタイムを短縮させます。したがって、工程間連携が重要となるのです。
工程間連携ができて初めて、機能別レイアウトでも各種生産指標設定が可能となります。
そうでないと各種生産指標はボトルネックになっている人や工程次第となり、設定ができません。先の幹部の言葉通りです。
工程間をスマートに活用するにはチームの力を磨くしかありません。それが規模を追わず、差別化で生き残る中小現場のスタイルです。
製品別レイアウトは自然発生的にはできません。製品別レイアウトには経営者の意志や意図が反映されるからです。経営者が望む能力を設定してレイアウトを組み立てます。
一方、機能別レアウトは「たまたま、結果的にそうなった。」という風に出来上がるケースも少なくないのです。徐々に工場を大きくした場合はそうです。
当初、できていた能力計算も徐々に難くなります。工程間が従来より増えるからです。
貴社の設備レイアウトを今一度眺めてください。能力計算ができていますか?できていなかったら工程間がスマートに使われていない証拠です。
次は貴社が挑戦する番です!!
成長する現場は、工程間をスマートに活用できるので柔軟性と生産性を高められる。
停滞する現場は、属人的な仕事のために工程間の存在が時間ロスの原因となっている。