「生産性ロードマップ戦略」—儲かる工場経営を目指して—第307話 成長モードの現場が物流で考えるべきことは?
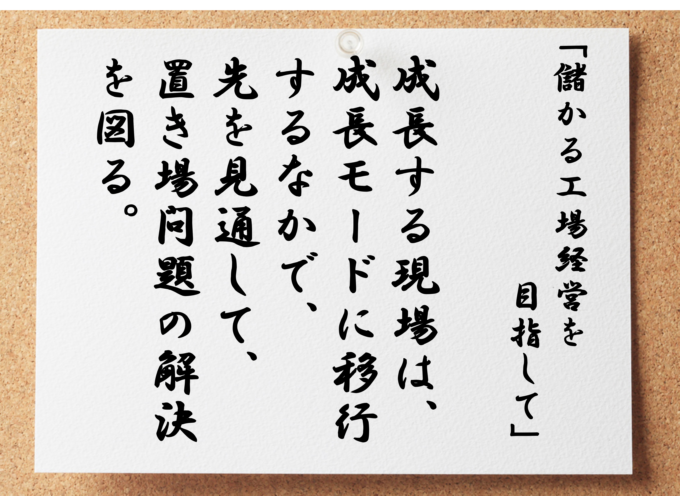
「置き場の土地を確保できるかもしれません。」
まさに今、事業を成長させつつある経営者の言葉です。
先代から事業を引き継いでからしばらくは苦しい時間でした。それでも踏ん張って試行錯誤しながら新規事業を探った経営者です。
腹を括った本気の経営者は必ず何かを引き寄せます。その後、コロナをものともせずに「売上高の右肩上がりが止まりません!」という成長モードに至りました。
成長モードに移行した現場で留意することがあります。先の経営者へそのことを伝えようとしましたが、既に動いていたようです。冒頭の言葉です。
工場には2つの流れがあります。
モノの流れと情報の流れです。
経営者は情報でモノをコントロールします。情報でモノを滞りなく流すのです。その体系と手順が工程管理に書かれています。工程管理がリードタイム短縮で欠かせない基礎知識であるとお伝えしている所以です。
経営者が直接にモノをコントロールしている現場は儲かりません。社長業に専念できないので当然です。
モノが現場を流れるときの姿は3つです。
・原材料
・中間製品(仕掛品)
・完成品
経営者は運転資金を最小化したいと考えます。したがって、スリムな工場経営では在庫削減を目指すのです。原材料、中間製品、完成品、3つの在庫が削減の対象となります。
モノの流動をよくして、停滞する時間を減らせば、3つの在庫を減らせます。スリムな工場経営では独自のタイムマネジメントが欠かせません。
在庫量とリードタイムは関連しています。特に中間製品(仕掛品)とリードタイムの関係は重要です。
成長モードを目指す経営者に必要なのは投資です。人と設備にお金を投じます。将来投資です。固定費の規模感はこの将来投資で決まります。
固定費は投資と考えるのです。原則、削減の対象にしません。「社長の夢の実現」に必要な投資だからです。
大手のように目先の収益確保を目的としたリストラをやってしまうと、回復時に苦労します。一旦、シュリンクした現場をもとに戻すのに時間を要するからです。
健全に拡大させる固定費は付加価値額で回収します。経営者が見通したいのは3年後、5年後、10年後に積み上げるべき付加価値額の規模感です。
工程管理を考える上で必要な数値が付加価値額の規模感で決まります。
それが物量です。
工場内を流動するモノの数量、重量、体積、長さ等々。工場レイアウトに影響する「物量」が明らかになります。
場内の物流が2倍になると、ざっくり在庫の規模感も2倍です。原材料、中間製品(仕掛品)、完成品の規模感です。
在庫規模感の決定要因にはサプライチェーンやお客様の事情もあるので、実際の在庫量は単純に決まりません。
ただ、そのなかでも中間製品(仕掛品)の物量は我が社でコントロールできます。それを決めるのがリードタイムです。物量が2倍でもリードタイムを半分にできたら中間製品(仕掛品)は従来と同じにできます。
2倍の物量をこなす設備があってリードタイムを半減すれば、場内の物流が2倍になっても、中間製品(仕掛品)を増やさなくてもいいのです。
中間製品(仕掛品)の数量抑制は経営者の思考回路に組み込みたい考え方です。
ただし、他の在庫要因はサプライチェーンやお客様の事情もあるので、いかんともし難いです。物流増と共に、原材料と完成品のスペースや空間は増えると考えるしかありません。
事業のステージが変わるのです。ちょっと片手間における場所があればイイやという水準ではありません。
原材料置き場や完成品置き場、出荷待ち品置き場等々。物量増に伴って置き場のスペースや空間を確保しなければなりません。
成長モードにある先の経営者に置き場確保の必要性をお伝えしようとしたのは、こうした事情があったからです。
成長モードに移行した現場ではスペースや空間が不足するかもしれません。起こってしまってからでは手遅れとなります。先手必勝の経営課題です。
場内で流動する物流が増えれば在庫増は避けられません。これまでの仕事のやり方でそのまま物流を増やすとそうなります。
原材料増+中間製品(仕掛品)増+完成品増
だからこそ、リードタイムの短縮です。
原材料増+中間製品(仕掛品)現状維持or微増に抑制+完成品増
独自のタイムマネジメントで場内を流動する物流をコントロールして仕掛品を増やさないようにするのが現場の王道です。
ただし、頭とお尻だけはどうしようもありません。必要なスペースや空間を確保します。
在庫は運転資金増につながるので、従来から「在庫は悪」との考え方がありました。特に仕掛品は「現場に眠っているお金」です。
経営者なら「1日でも早く完成させて、お客様から検収あげよ!」と言いたくなります。また原材料や購入部品も同様です。製造に合わせてタイミング良く買うように!と指示を出したくなります。
こうした在庫最小化の原理原則は普遍ですが、昨今の外部環境を踏まえると考え方を変えなければならなくなったようです。
ジャストインタイム(JIT)は必要なものを、必要なときに、必要な数量を納品してもらうためのやり方です。これは在庫を減らす手法でもあります。
ただ、当然のことですが、これはサプライヤーが必ず納期通りに納入してくれることを前提としています。
しかし、新型コロナによるグローバルサプライチェーンの機能不全や中国でのロックダウン、そしてロシアによるウクライナ侵攻などにより、この前提条件が崩れました。
納期通りにモノが届かなくなったのです。グローバルに変化しつつあります。在庫を持つメリットがデメリットを上回るようになりました。
在庫を持つメリットがデメリットを上回るようになったのなら、戦略的に在庫を増やすことを考える必要があります。スペースの確保も課題です。
在庫を最小化したが、お客様への納入が不安定になるようでは、なんのための在庫最小化かわかりません。本末転倒です。在庫も必要経費という状況に変わりつつあることには注意を要します。
原材料や必要な部材を納期通りに手にすることがドンドン難しくなる懸念もあります。ますます、在庫を置くスペースや空間が必要になるかもしれません。
経営者は変化を読んで、それに対応しなければなりません。思い付きではなく、戦略的に置き場も考えます。
先の経営者は先手を打って置き場を確保しました。不確定要素がまだあるようですが、良い方向へ進むことでしょう。腹を括った本気の経営者は必ず何かを引き寄せます。
次は貴社が挑戦する番です!
成長する現場は、成長モードに移行するなかで先を見通して置き場問題の解決を図る。
停滞する現場は、増える物量に対して片手間の対応しかしないので現場が狭くなる。