「生産性ロードマップ戦略」—儲かる工場経営を目指して—第312話 品質管理ではお客様の協力を仰いでいるか?
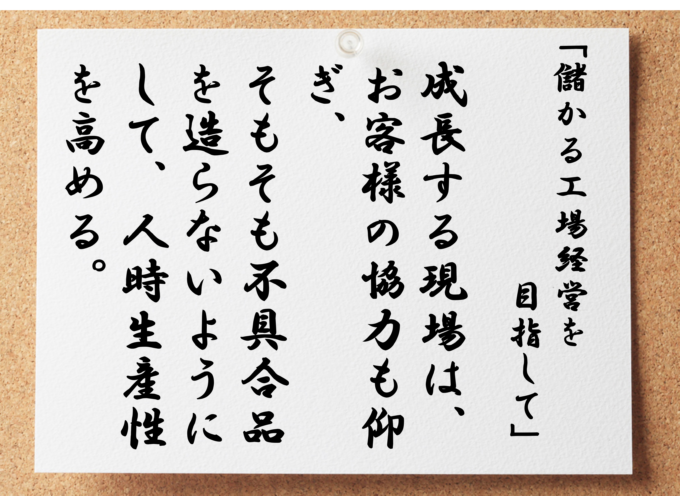
「お客様が事前に決めてくれないからです。」
装置メーカー製造部門幹部の言葉です。
品質クレームが毎月発生しています。原因を分析すると溶接不具合など製造過程に問題があった事例に加えて、お客様にも責任の一端があると思われる事例がありました。受注決定時に未確定の仕様項目があったりするのです。
未確定の仕様項目について、製造後に、見込みと異なることを要求されると、作り直しになります。そうした事例もお客様はクレームだと認識しているのです。幹部も困っています。
冒頭の言葉です。
事情があるにせよ、お客様が品質クレームであると認識しているなら対策を打たなければなりません。商習慣だからと言って、それを放置するようではダメです。
こうした品質管理業務がしっかり為されていないと、リードタイム短縮どころではありません。人時生産性を高めたかったら、まずは品質管理です。
お客様に迷惑を掛けながらの生産性向上は儲かりません。
品質管理の論点は2つあります。
・不具合品を流出させない
・そもそも不具合品をつくらない
不具合品を流出させるとお客様に迷惑をかけてしまいます。品質クレームです。品質クレームを起こしてしまったら、コストを度外視して対応しなければなりません。
また、流出させないまでも、不具合品をつくってしまうと、作り直しや手直しが必要になります。リードタイムが余計にかかる分、納期遅延のリスクが高まるのです。納期遅延すれば、当然、お客様に迷惑が掛かります。
品質問題は自社の収益性を低下させるだけでなく、お客様にも迷惑をかけるのです。経営者は後者の影響に留意しなければなりません。信用を失うのは一瞬です。
不具合品を流出させないために検出能力を向上させます。つくってしまった不具合品を検出しなければなりません。具体活動は出荷検査や工程内検査です。
そして、そもそも不具合品を造らないために品質作り込み体制を構築します。製造着手前には、試作や初物処理、初期流動管理などが具体活動です。製造着手後には、自主検査や設計品質フィードバック、工程変更管理などが具体活動です。
こうした取り組みにはコストがかかります。しかし、コストがかかるからと言ってやらなければ、不具合品が発生し、作り直しや手直しのコストがかかるのです。そして、品質クレームを引き起こしてしまったら、それに対応するコストがかかります。
品質コストは下記で定義できます。
品質コスト=(評価コスト+予防コスト)+(外部失敗コスト+内部失敗コスト)
・評価コスト:検出能力向上費用
・予防コスト:品質作り込み費用
・外部失敗コスト:品質クレーム対応費用
・内部失敗コスト:作り直しや手直し費用
(評価コスト+予防コスト)と(外部失敗コスト+内部失敗コスト)はトレードオフです。前者を増やせば、後者が減ります。前者を減らせば、後者が増えます。
品質コストはお客様に迷惑を掛けないための費用です。しかし、儲けに直接、つながるわけではありません。不必要にかけすぎては儲けも減ります。
必要にして十分な品質コストを見極めるのが大切です。経営資源に制約がある中小製造現場ならなおさらです。具体活動を分類すると下記の①、②、③です。
・不具合品を流出さない①製造着手後の活動
・そもそも不具合品を造らない②製造着手前の活動と③製造着手後の活動
全て必要な活動ですが、直接工数以外に工数を割くことが難しい中小現場で効果的な活動があります。それは②です。そもそも不具合品を造らない②製造着手前の活動。
まだ製造する前の取り組みなので、未然防止ができます。最小コストでお客様に迷惑をかけずに済ませられるのです。品質コストの考え方は品質活動のやり方を示してくれます。
先の企業で起きているクレームを分析すると、お客様側での想定外の使い方や新たな仕様の追加が原因になっていることがありました。
したがって、品質クレーム原因の一端はお客様にもあることは明らかです。ただ、お客様の認識が品質クレームとなっている以上、悪いのは供給側となります。
先の企業には「後出しじゃんけんのように言われても・・・」との言い分があります。しかし、お客様が品質クレームと考えているのでどうしようもありません。全ての決定権はお客様にあるのです。
それが嫌なら、自ら決定権を持てる下請け型モデルか自社製品で直接に市場に向かう商売に変えるしかありません。
事業モデルを変えないのなら、起こっている事象を品質クレームと認識されないように先手を打つばかりです。「後出しじゃんけん」をされないようにします。新規製品を受注する際の取り決め事項を明確することです。商習慣の見直しです。泣き寝入りはやめます。
品質上の要求事項が後出しじゃんけんのようになっているために、苦労している現場が少なからずあるようです。経営者はこうした状況を放置してはいけません。
品質管理の考え方を徹底できないからです。お客様に相談しながら、あるべき姿に変えます。あるべきやり方は納期遅延を未然に防ぐとともに、リードタイム短縮を可能にします。
品質管理の2つの論点
・不具合品を流出させない
・そもそも不具合品をつくらない
これらはお客様に迷惑を掛けないための論点でもあります。お客様にも協力をしてもらわなければなりません。商習慣に囚われず、見直すべきことは見直すのです。
これができて初めて、本当の品質管理ができます。特に製造着手前の活動は効果的です。お客様にも協力を仰いで「そもそも不具合品をつくらない」ようにします。前向きの提案に反対するお客様はいません。
次は貴社の番です!
成長する現場は、お客様の協力も仰ぎ、そもそも不具合品を造らず人時生産性を高める。
停滞する現場は、お客様の後出しじゃんけんに振り回され品質管理が全くできていない。