「生産性ロードマップ戦略」—儲かる工場経営を目指して—第330話 自動化の対象は製造現場だけではないのを知っているか?
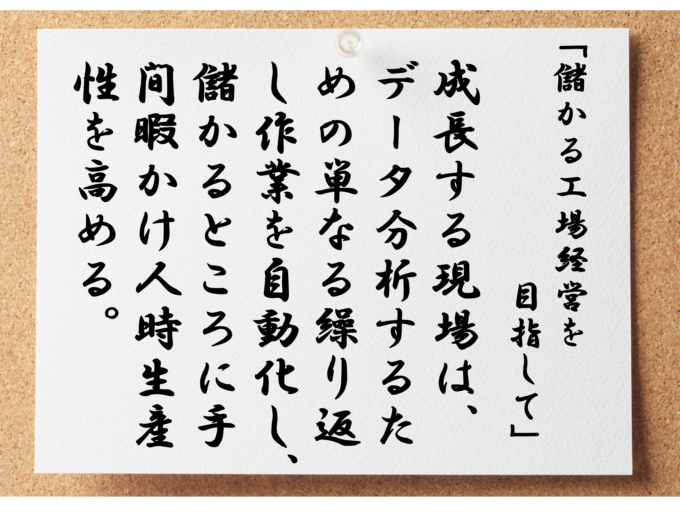
「現場でやれるようにしないといけませんね。」
人時生産性向上活動を現場へ定着させたいと考えている50人規模製造企業経営者です。
「納期遵守以外の仕事は定着しにくい」ことに気付きました。一方的にヤレ!と声を掛けるだけでダメだったのです。
人時に関連した納期以外の成績を示さなければ、現場も動きようがありません。
そうであるなら日々、成績を見せられるようにしたくなります。そこで、経営者自身でデータを分析しはじめました。
・・・・が、このやり方でいいのだろうかと?疑問が湧き始めたところです。
データ分析のお陰で状況を客観的に見ることができます。しかし、その結果を得るのに自身の時間を割かなければなりません。
社長には社長業というそもそもやらなければならない業務があります。それに対する経営者の答えが冒頭の言葉です。
事業の成長発展には利益が必要です。利益の多寡が儲かる工場経営の重要な指標であるのは論を俟ちません。利益が出るのか?出ないのか?経営者は常に判断できなければなりません。
利益は付加価値額-固定費です。経営者は、付加価値額(スループット)と固定費を管理します。
固定費は年に一回、社長が決めます。その後は毎月の決算で精度を高めれば十分です。一旦決めれば大きく変わりません。文字通り「固定」費です。
一方、付加価値額は変動します。販売数量は変動するからです。また昨今は、原材料が大きく変動しています。さらにはそれに伴って単価アップも大事になってきました。
付加価値額の変動要因をリアルタイムに把握し、それを即、計算へ反映させる必要があります。今、どうなっているのかが分からなければ適切な判断ができません。
販売活動や製造活動は日々です。したがって、日々、付加価値額は積み上がっています。利益が出るのか?出ないのか?付加価値額の積み上げ状況を日々知ることが要点です。
日々是決算です。
付加価値額の積み上げ状況は何で決まっていますか?
付加価値額積み上げのボトルネックは何ですか?
それを整理することからです。付加価値額積み上げは、販売活動と製造活動から構成されます。両者は切り分けて考えなければなりません。
工場での付加価値額積み上げ状況は製造活動で計られます。したがって、販売基準ではなく、製造基準で数値を揃えることが必要です。損益計算書の数値とは異なります。そもそも、損益計算書はリアルではありません。
そしてリアルに状況を知るためのデータを揃えるのです。自然と下記の方針になります。製造活動の目的は「効率よく造る」ことにあるからです。注目する指標も特定されます。
・現場には時間と人員数の制約があるから、積み上げ状況の成果は人時生産性に表れる。
・原則、分母を一定として、分子を積み上げることが要点になる。
・分母一定で分子を積み上げるには、詰めて、空けて、取り込むしかない。
・リードタイムを短くして、ドンドン新たな案件をこなし、人時生産性を高める。
・そこで、製造ロット毎の工数とリードタイムを継続的に収集する。
・一方で単価、@材料費、@外注費には外部環境変化を即刻、反映させる。
最後の2つがしくみ化の要点です。熱心な経営者程、ご自身でこの2つをやろうとします。ただし、それではダメです。経営者には新たなお客様とご縁を結ぶ重要な仕事があります。
付加価値額の積み上げ状況を見えるようにすることは儲かる工場経営に欠かせません。欠かせないのですが、経営者がそれをやったからと言って、直接に儲かるわけではないのです。
・新規のお客様とご縁を結ぶこと。
・既存のお客様から新規の受注をいただくこと。
これらは外の仕事です。社長にしかできません。
付加価値額の積み上げ状況を知ることはあくまで内の仕事になります。そうであるなら、内の主役である現場キーパーソンにやってもらうのが理に適っているのです。
経営者が不在でも工場を回せるようになることをしくみ化と言います。
付加価値額の積み上げ状況を見えるようにする際、データ収集から積み上げ状況の分析までのしくみ化が大切です。
1)現場実績のデータ化
2)データの集計
3)集計されたデータの分析
これらを業務として現場に定着させる必要があります。表計算ソフトを活用すればできる業務です。
現場実績のデータ化では、現場には定義に基づいた作業日報を書くように指示します。定義が大事です。
そして現場から上がってきた作業日報の数値を表計算ソフトへ打ち込ませます。データを集計しなければなりません。
そして、製造ロット毎、お客様別、商品別、担当者別、生産ライン別等々の分析です。打ち込んだデータを加工し分析します。
こうやって状況の見える化ができるのですが、問題があります。
精度と手間暇です。
例えば、3)集計されたデータの分析。
・データ加工の過程でコピペするうちに間違う。
・そもそもこの工数が惜しい。
経営者が考えた計算式に従って、現場のキーパーソンに間違いなくデータを処理させたいのですが、手作業ではミスも生じます。気を付けても間違えるのは人間です。
それに、そもそも現場のキーパーソンがこうした作業に時間を割いても、儲けに直接は貢献できません。間接作業だからです。
こうした作業も自動化の対象です。自動化の対象は製造プロセスだけではなく、データ分析の処理作業などの繰り返し業務にもあります。少数精鋭の中小現場ならなおさらです。
RPAによる事務処理の自動化が言われて久しいですが、ここまで大げさになる必要はありません。変化の激しい中小製造企業では、ある程度、手作業の部分を残しておくことも柔軟性を維持するのに欠かせないのです。
既存のツールを上手に使いこなせば、精度と手間暇の問題は解決できます。
独自のシステムを構築する。
市販のグループウェアや生産管理ソフトをアレンジする。
表計算ソフトのマクロを活用する。
表計算ソフトをプログラムで処理する。
しくみ化の初手は手作業です。そうして見える化のロジックを理解させます。車の運転もマニュアル車から覚える方が本質を理解できるのと同じです。
ただ、全てが手作業では精度と手間暇の問題が残ったままです。そこでデータ分析の自動化を考えます。
最終的に独自システムです。ただ、見える化の体系は使い込まないとできあがりません。システムには改訂に改訂を重ねる大事な「儀式」が待っています。
大手のようにシステム専任がいれば、最初から独自システムに取り掛かってもかまいません。ただ少数精鋭の中小製造企業ではダメです。順番にやります。
まずは市販のソフト、マクロ、プログラムの活用です。使えるものを使います。いわゆるDX化。こうしたことにも挑戦です。
ご支援先でもDX化への対応はいろいろあります。問題が解決済のところもあれば、慣れなくて苦戦するところもあって様々です。ただ、ここは心配するところではありません。
できないものはできる人にやってもらえばいいのです。時間をお金で買ってさっさとできるようにします。外部に専門家がたくさんいるはずです。
弊社も、ご支援先の要望に応じ、必要ならば経営者と一緒にプログラムを考え、簡易的な自動化をやってもらっています。
儲かる本質はここにはありません。さっさとやってしまうだけです。
付加価値額の積み上げ状況を見えるようにする際、データ収集から積み上げ状況の分析までのしくみ化が大切です。
ただ、要点はそのしくみにあります。プロセスで処理される作業自体に価値はないことには注意して下さい。
分析それ自体は大切ですが、分析のための処理業務は単なる繰り返し作業にしかすぎないのです。それ自体は儲けに貢献していません。
したがって、こうした単なる繰り返し作業は可能な限り自動化して、精度と手間暇の問題を解決するのです。自動化の対象は製造現場だけではありません。
儲かるところには手間暇かけます。繰り返しの作業は現場であろうが事務処理であろうが自動化を考えるのです。儲ける現場は時間を無駄にしません。
儲かる現場は、どこに手間暇を掛ければ儲かるのかを知っています。データ入力やコピペだけを繰り返し淡々とやっているだけでは儲けに貢献していないことに気付くはずです。
次は貴社が挑戦する番です!
成長する現場は、データ分析も自動化し、儲かるところに手間暇かけ人時生産性を高める
衰退する現場は、儲からない業務でも淡々と作業しているので人時生産性が高まらない