「生産性ロードマップ戦略」—儲かる工場経営を目指して—第331話 現品管理の水準で評価できる大事なことは?
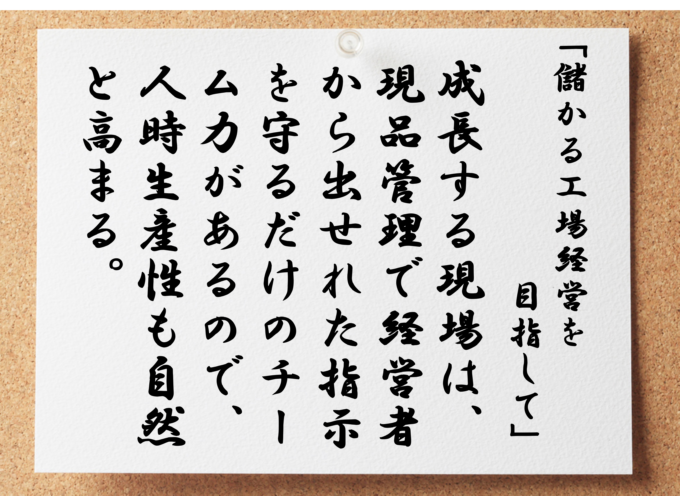
「指示を出しますが治具類の管理ができていないですね。」
先日、ご相談をいただいた、年商3~4億円規模中小製造企業、経営者の言葉です。
現在、一定水準の収益を確保している経営者です。ただし、現状に満足していません。意欲的な経営者とはそう言うものです。弊社のメルマガをご覧になり、まだまだやることがありそうだとお考えになりました。
既に現場活動をやっているものの、儲けにつながっている感じがしません。やり方を変えなければと考えてのご相談です。
当方から現品管理の状況を伺ったときのことです。現品管理の要点をいくつかお伝えした後、「う~ん」という感じで、言葉が返ってきました。冒頭の言葉です。
工場には2つのモノが流れています。情報と現品です。情報の流れで現品の流れを管理します。ファブレスであろうとなかろうと情報の流れはなくなりません。
ただし、ファブレスでは現品の流れがありません。自社工場を持たないので委託先にやってもらいます。自社工場には投資が必要です。ファブレスはその固定費を変動費化します。資本の効率を高める製造業、ひとつのあり方です。
したがって、製造業で現品を扱う道を選択したのなら、現品の流れをきちんとしないといけません。ファブレスにおもいっきりおいてけぼりを喰います。製造業はグローバルで戦っているのを忘れてはなりません。
現場をもって、自ら原材料を加工し「価値」を加え、積み上げて稼ぐ醍醐味を味わいたいので私たちは現品を扱っています。そうであるなら現品の流れを管理する必要があるのです。
現品を扱う道を選択した私たちは、ファブレスが現品を扱う手間暇を嫌っているのを逆手に取り、現場で現品を扱うメリットを最大限に享受しなければなりません。
ファブレスでは手にできない、メリットをしっかり手にできていますか?そのために必要なのが現品管理です。
何がどこに、どれだれ、次は?
これが現品管理です。
位置管理
数量管理
流動管理
3つあります。
商品、製品だけでなく、治工具類、金型などの製造過程で扱う道具も対象です。
工場のスペースには制約があります。制約があるので、物の置き方を決める位置管理の重要度は自然と高まります。
多くの現場で目にする形跡管理は位置管理のひとつです。形跡管理は治工具類を保管するやり方としてしばしば目にされます。
ボードにハンマーやスパナ、レンチなどの「形状」を描き、該当する治工具をそこへ掛けて保管するやり方です。使う時も戻す時も場所が見えやすくなっています。使用中はありません。ずっとなければ、戻し忘れているとわかります。目で見る管理です。
位置管理として、置く場所を指定するロケーション管理も多くの現場でやられています。置き場を決めて、それ以外は置かせないようにするやり方です。
エリアを決めて、その範囲内に特定の物を置かせます。エリアだけ指定するfreeの場合と、エリアの中で場所も特定するfixedの場合の2つです。
形跡管理、ロケーション管理、どちらの場合にしても置き場管理者を設定し、ルールを守らせます。
形跡管理もロケーション管理も、5Sに基づく現品管理です。ルールを決めて、全員が守らないと管理になりません。物の置き方を見れば現場の躾水準が分ります。
5Sに基づく現品管理の他に、仕組みに基づく現品管理もあります。物品の流れでそうやらざるを得なくなるやり方です。
例えば、押出型と引張型の在庫管理がそうです。管理者が特定されます。引張型では、管理者がしっかり管理しないと自分で自分の首を絞めてしまうので、仕組み上、押出型より管理の実効性が高いです。
先入れ先送り管理も仕組みに基づきます。仕掛品を場内に複数並べて置くとき、壁と垂直になるのを避けます。導線に沿って置けば次工程への移動が楽です。フォークリフトの右往左往がありません。
一般的に仕組みによる現品管理の置き方はプラントレイアウト時に設定されます。工場スペースは制約があるからです。
効果的な置き方は効果的な導線でも決まります。工場やラインを設計するときに検討される項目です。
改善活動で置き方の根本解決はできません。プラントレイアウトを検討する際は衆知を集めることになります。この時点で現場での仕事のやりやすさの8割は決まるのです。
位置管理は現品管理の基本です。ファブレスとは異なり、現場で形があり重量がある「現品」を大量に扱います。手間がかかるのです。
そのうえ、運搬と停滞は価値を生みません。したがって、現品管理は最小コストでスマートにやらないと、付加価値額積み上げの足を引っ張ることになります。
現品票だけでは難しいから、現場の協力も得て、置き方でも管理をするのです。経営者はこのあたりの事情を作業者へ説明する必要があります。説明しないと現品管理の重要性が伝わりません。
多品種少量生産現場では異品混入のリスクが高くなります。絶対に起こしてはならないことです。だから、経営者が説明しなければなりません。
そして、5Sに基づく位置管理にせよ、仕組みに基づく位置管理にせよ、どちらもルールに従ってやられます。ルールを徹底できない現場では現品管理ができないのです。
先の現場では形跡管理ができていません。そして、位置管理はルールに基づいてやられます。それができないと言うことは、決められたルールを守れない現場ということです。
指示どおりにやらない。
ルールを守れない。
現場がこうした状況になっていませんか?こうした状況になったとき、経営者や幹部はどうしていますか?
昔から、言っても長続きしないし、いつの間にかうやむやになっている・・・・。
もし、今、こうなら改めないとダメです。
経営者や幹部から出される指示やルールは、無理にやらなくてもいいのだと経営者や幹部自身が現場へ教えているようなものですから。
自分にとって難しいこと、できないことは無理してやらなくてもいいのだと現場は普通に考えます。現場が悪いのではなく、自分で発した指示やルールの進捗を確認せず、できなければまぁしょうがないと考える経営者や幹部に責任があるのです。
経営者や幹部が発する指示やルールがないがしろにされる現場で改革は出来ません。
「変える」とはビフォーを捨てることです。そしてアフターは当然ですが、多くの場合、現場にとって無理難題となります。競合と同じ事ことをやっていても儲からないからです。
したがって、ルールを守れないのを放置していると、いつまでたってもできることしかやらない現場のままです。行く末が見えています。
指示のフォローやチェックができていません。PDCAを回せない中小製造企業の末路。人時生産性が高まるはずがありません。
弊社ではプロジェクトを通じて、右腕役や現場キーパーソンにルールを守らせる機微を理解してもらっています。チーム力が大事です。
そもそも、ルールとは全員で守るものです。現品管理の具合で現場のチーム力を測れます。貴社はどうですか?
経営者や幹部から出された指示やルールを守れない現場のチーム力はたかが知れています。現場改革、意識改革、構造改革はまずむりです。躾水準の話にとどまります。改革どころではありません。中小製造現場にまん延している属人的なやり方に甘んじることになります。
目で見える目の前の現品管理もできない現場が、改革をやり切るとは思えないのです。
現品管理は目で見てすぐ分かります。現場のチーム力水準を評価するのにも最適です。現場での位置管理状況を確認してください。気付くことがあるはずです。
次は貴社の番です!
成長する現場は、現品管理でルールを守れるだけのチーム力があるので人時生産性も高まる
衰退する現場は、現品管理もあいまいでなんとなく属人的にやっているから改革はできない