「生産性ロードマップ戦略」—儲かる工場経営を目指して—第350話 標準書を実務で役に立たせる要点を確認したか?
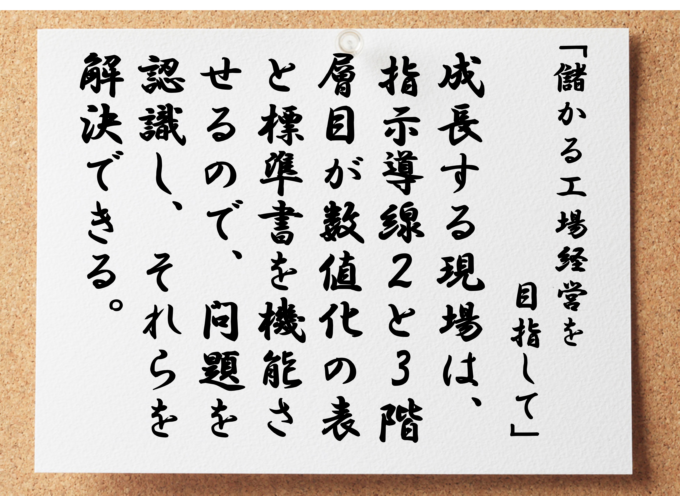
「先生、指示の出し方が十分ではなかったようです。」
先日、個別相談をいただいた素材メーカー経営者の言葉です。
腰を据えた現場活動をやりたいと考えています。これまでも現場キーパーソンへ指示を出してきました。しかし、取り組みはとん挫の繰り返しです。
現場キーパーソンの仕事ぶりに問題があります。ただ、だからと言って現場が悪いわけではありません。そのやり方がわからないだけです。
教わることなく、人時生産性向上の具体手段を知っている従業員はいません。抽象的な課題だからです。経営者と従業員の目線の高さは異なります。
現場キーパーソンへやり方を教えるのは経営者の仕事です。さらに正しく指導しなければなりません。先の経営者はあることに気付いたようです。冒頭の言葉です。
人時生産性を高める手順があります。中小製造経営者が最初にやることは分母一定、分子積み上げです。間違っても分母増から始めてはいけません。
大手のようにプラントレイアウトで目標LT、CTを設定し現在に至っているなら分かります。そうした現場は、概ねじゃぶりつくされているからです。そうであるなら、人時生産性を飛躍的に高める方法は原則、設備投資しかありません。
一方、今まで、工場を“成り行き”で成長させてきたのなら、今一度立ち止まる必要があります。まずは現状を把握して欲しいのです。
把握するための環境整備をしてください。そうして、現場をしゃぶりつくすのです。大手と違って中小にはいろいろな制約があります。だから生き残るための初手はこれです。
環境整備のひとつに見える化があります。人時生産性を高めたいわけですから、人時生産性が見えなければなりません。
さらに人時生産性向上に貢献する項目を見えるようにします。人時生産性向上と因果関係がある項目です(相関関係ではありません)。
風が吹けば桶屋が儲かる理論に従って項目を抽出します。
LTは外せません。工数も必要です。特注品/規格品識別も必要かもしれません。経営者が考え、分析して、項目を選びます。ここの選択は大切です。
我が社の共通用語形成につながります。
経営者が見える化したい項目を選択した後、項目を数値化するのは現場の仕事です。
作業時間、段取り時間、発注LT、刃具交換間隔、仕掛品停滞時間、稼働率、可動率、良品率・・・QCDが複雑に絡み合っているのが製造業です。
そこに貴社独自の組織風土、文化、やり方が加わります。数値化のやり方は貴社独自にならざるを得ません。
したがって見える化では、数値化の具体手順を決める必要があるのです。そこを決めないと定義不明の数値化になってしまいます。共通用語が大事です。
見える化=数値化の目的は判定です。
・増えたのか?
・横ばいなのか?
・減ったのか?
判定したら、アクションを起こします。PDCAのCAに相当する行動です。人時性生産性向上に貢献する項目がよくするとともに、数値が悪化していたら手を打って問題を解決します。ISO9001で求められている継続的改善です。
・数値化すること。
・アクションを起こすこと。
先の経営者の現場ではここに問題があったようです。
現場は社長指示にしたがって、表を埋めてさえいればイイと思い込んでいました。変化を知ってアクションを起こす水準に至っていません。
裏返して言えば、指示されないことはやらない現場とも言えます。先の経営者の悩みはここです。経営者が一から十まで言わないと現場は動けません。
先の経営者は、出来高と手間暇の推移を数値化して、問題を見つけようとしました。問題が数値で示されれば、現場キーパーソンは問題を解決したくなるだろうと期待したのです。
しかし、残念ながら、手渡された数値化の表を埋めるだけに留まっていました。指示されないことはやらないという思考回路に問題があります。
「社長指示にしたがって仕事をすればイイ」=「指示されないことはやらなくてもイイ」と誤解している現場キーパーソンがいるなら、正しい姿勢を教えなければなりません。
経営者は外での社長業に専念したいと考えます。そのために、現場キーパーソンが経営者に代わって工場の仕事を仕切るのです。
数値化の表を埋めるのは作業者の仕事です。
そして、作業者が数値化の表をきちんと埋めているかどうかを確認すること、数値変化を捉えること、問題を認識したらアクションを起こすこと、そして問題を解決すること、これらが現場キーパーソンの仕事です。貴社独自の体系になります。
経営者は現場キーパーソンへこの体系を教えなければなりません。「数値化の表」を現場キーパーソンへ手渡しして、後は、寝て待っていれば果報が届くというほど、人時生産性向上の取り組みは単純ではないのです。
現場キーパーソンが自分で数値化の表を埋めて満足しているようでは自身の役割を理解していません。
・数値化の表を確認すること
・変化を捉えること
・問題を認識してアクションを起こすこと
・問題を解決すること
現場キーパーソンの仕事をはっきりさせます。
例えば、数値化の表の使い方も明文化する必要があるということです。手順書、標準書がそれです。
・誰が数値を記入するのか?
・いつ記入するのか?
・誰が記入した数値を確認するのか?
・どうやって問題を認識するのか?
・問題を認識した人は何をどのするのか?
現場業務の多くは図表と標準書の組み合わせで説明できます。
1.数値化の図表
2.標準書
標準書で使い方を明文化して現場へ浸透させるのです。
先の経営者の場合、標準書作成の指示が抜けていました。ここの具体指示が足りなかったのです。
現場のキーパーソンは自分の思考回路に基づき、自分の判断基準でやることになります。それが「指示されないことはやらなくてもイイ」でした。
標準書がなければそうなります。この思考回路では指示導線4階層を機能させられません。経営者は忙しいままです。
現在ご支援中の幹部が先日、次のことを語っていました。
「誰がいつ記入するのか?それを誰が確認するのか?と繰り返し言って聞かせたのですが、期待通り行動してくれません。」
数値化の表で変化を知ろうとしている幹部です。熱心に「口頭」で指示を出していました。しかし、そうならないようです。
「口頭」がだめなら「文書」で示すしかありません。
標準書とはその現場のお作法や手順を説明したものです。新人作業者も含めて誰でもそうしなければなりません。経営陣から届いた指示をうまくこなすやり方が書かれています。
・安全に留意しながら手離れのいい作業をして欲しい
・データを活用するので作業日報はきちんとつけて欲しい
・段取り作業はバラツキのないやり方をやって欲しい
等々、「そうして欲しい」は経営陣から出されますが、それを実践するのは現場です。したがって、具体的なお作法を決めるのは現場になります
つまり標準書を作成するのは現場です。
標準書の要点は判断基準です。判断基準=「そうして欲しい」。判断基準は経営陣から降ろされます。トップダウンです。
その判断基準に従って、うまくこなすやり方は当事者が考えます。いわゆる現場の自発性はここで発揮されるのです。自分勝手と自発性の違いは判断基準の有無にあります。。
したがって、指示導線4階層が機能していないと実践的な標準書はできません。実践的標準書のキモは上から2階層目と3階層目の仕事ぶりにあるからです。
3階層目が標準書を作成し、きちんとやっていない作業者がいたら、3階層目が指導します。そして2階層目が問題を認識してその解決を図るのです。
数値化の表と標準書が実務で役にたっている工場にはしっかりした指示導線があります。
数値化の表と標準書の主役は2階層目と3階層目です。人材を見極めます。訓練、訓練、訓練。プロジェクトの実務を通じてスキルアップしてもらうのです。
2階層目と3階層目で最適人材不在となると、経営者は辛いです。そもそも実践的な数値化の表と標準書ができません。できたとしても機能させられないのです。現場は人なり。
先の経営者は問題の本質に気付いたようです。
次は貴社の番です!
成長する現場は、指示導線2と3階層目が数値化の表と標準書を役立たせて問題を解決する
衰退する現場は、表を埋めればイイとだけ考えているので相変わらず問題が解決しない