「生産性ロードマップ戦略」—儲かる工場経営を目指して—第369話 現場に「比べる」を教えているか?
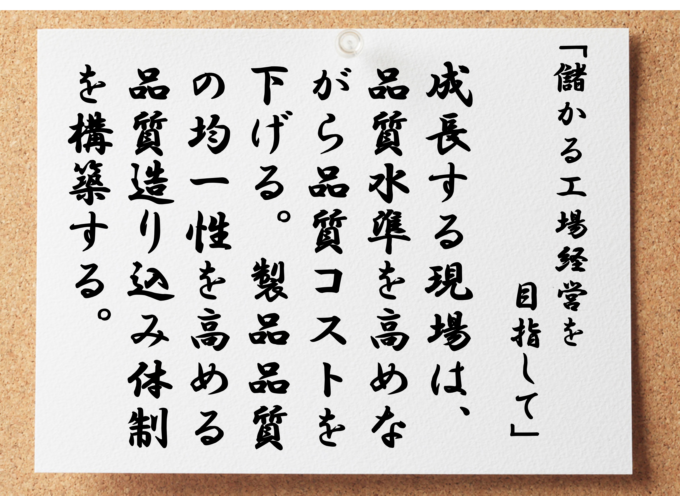
「抜き取り検査への判断基準はありますか?」
人時生産向上活動に着手して3年目、中堅製造企業工場長の言葉です。
これまで諦めないで試行錯誤してきた工場長です。頑張る人には大きな力が働きます。自発的な改善活動が現場に定着してきました。
売上高移動累計も底を打ち、徐々に右肩上がりの傾向を示しています。人時生産性移動累計も同様です。並行して進めてきた品質改善活動でも不良率が低下しています。数%水準から1%以下で安定してきました。
品質コストの考え方を理解している工場長です。収益への貢献がもっとできないか考えています。経営者が頼りにしている右腕役らしい仕事ぶりです。
これまで学んできたことを血や肉にしてきました。冒頭の言葉です。
品質管理には2つの観点があります。
・品質不具合品を流出させないこと
・そもそも品質不具合品を造らないこと
前者の課題は検出能力を上げること、後者の課題は品質造り込み体制をつくることです。
品質不具合品を流出させると常時にはないコストが発生します。選別工数や関連費用、お客様のところへ出向く出張費用、代替品製造費用などです。外部失敗コストと言われます。ただ、この場合、信用の毀損はコスト以上の損失であることを忘れてはなりません。
また、品質不具合品を発生させると、それ自体でもコストが発生します。スクラップの管理や払い出し、そして造り直しのコスト。手直し品なら管理費用や手直し費用です。内部失敗コストと言われます。
こうした失敗コストは最小化しなければなりません。そこで、評価コストを掛けて検出能力を高めます。さらには、予防コストを掛けて品質造り込み体制を強化します。
評価コストや予防コストで失敗コストを低減できるのです。逆に評価コストや予防コストをケチれば失敗コストが増える懸念があります。
評価コスト+予防コストと失敗コストはトレードオフの関係です。両者のバランスで品質コストが決まります。そのバランスを維持しながら、品質コスト全体を小さくするのが現場で行われている品質改善活動です。
多くの現場では不良品を減らそうと頑張っています。不良品が発生する原因を究明し対策を考え、それを実行して効果を確認するのです。
効果を確認するのに使われるのは不良率です。改善活動ではビフォーとアフターを比べます。不良率が小さくなれば効果があったと確認できるので、そこで従来の作業標準(ルール)を変更するのです。
そうやって品質改善PDCAを回します。
品質造り込み体制では、不良率を指標として、評価コスト+予防コストを睨みながら失敗コストを小さくしていくのです。
品質に限らず改善活動では共通用語となる指標が欠かせません。比べるためです。
不良率を小さくして失敗コストを低減できれば非価値時間を減らせます。工数当たり正味作業時間を増やすことで人時生産性向上につなげられるのです。変動費低減の直接的な効果も期待できます。品質造り込み体制での品質改善初手は不良品を減らすことです。
失敗コストを最小化します。
ただし、儲かる工場経営の品質管理はここでは終わりません。品質コストを低減するため不良品をさらに一層、減らします。そして、失敗コストを減らす段階を卒業した先にあるのが、製造品質の均一性を向上させる取り組みです。
製造品質の均一性が高ければ不良品や手直し品が発生する懸念が減ります。その分、検査の手間暇を省いても問題ないだろうと考えるのは自然なことです。論理的な考え方に基づいて検査の手間暇を省く分には構いません。
先の工場長もそう考えました。その考え方自体はイイのですが、正しい知識に従ってやらないと火傷をします。
製品品質の均一性を確認する指標が工程能力指数です。
指標の多くは分数で表記されます。分数なので分母と分子です。分母と分子で「効率」や「比較」を示してくれます。
人時生産性や利益率は効率です。工数や売上高に対してどれだけの付加価値額や利益を生みだしたかを示しています。
一方、不良率や手直し率は比較です。加工した個数や検査した個数と不良品や手直し品の個数を比べて、多いとか少ないとかを示しています。
工程能力指数は不良率や手直し率と同じく後者です。分母と分子を比べています。
不良率
・不良品数/加工数
工程能力指数
・規格幅/バラツキ
・差/バラツキ
・ズレ/バラツキ
バラツキと規格幅や差、ズレを比べているのが工程能力指数です。不良率では加工数と不良品数を比べています。
工程能力指数は製品品質の均一性を数値化したものです。不良率や手直し率と異なり数値が大きいほど良好と判断されます。
工程能力指数で目安にする数値が1.33です。
この数値に至れば「工程能力がある」とされます。
「工程能力がある」では具体的に何ができるのか?
評価コストの削減です。
例えば、全数検査を抜き取り検査に移行させることが考えられます。
全数検査から抜き取り検査への移行による収益アップへの貢献は小さくありません。検査工程はボトルネックになりがちです。それを解消できます。さらには品質コストに占める評価コストの直接的、間接的削減です。
「工程能力がある」品質水準では評価コストを削減する機会を手にできます。
ただし、工程能力指数1.33の不良率水準は加工数10万個に対して不良品数3個か4個であることを知らなければなりません。加工数100個や1,000個に対して不良品が1個、10個の水準とはけた違いです。
先の現場では加工数1,000個、10,000個に対して不良品は数個という水準でした。工程能力がある水準ではありませんが、数%水準で語る不良率と比べれば良好であるとは言えます。
しかし、工程能力があるとは言えず、抜き取り検査への移行は慎重さが必要です。工程能力の考え方を加え、評価コスト低減のやり方を抜き取り検査の手順から考えることにしました。
品費造り込み体制における品質改善の初手は失敗コスト低減です。不良率や手直し率です。不良品や手直し品を減らします。加工数100個、1,000個で10個程度発生する不良品や手直し品を対象にした品質改善です。
その水準の不良率や手直し率を卒業したら工程能力指数です。加工数10万個に不良品数3個か4個の水準に挑戦します。評価コストを下げる機会を手にできるのです。
品質水準を高めながら品質コストを下げます。
品質造り込み体制の思想はココにあります。
そもそも不具合品を造りません。
「なるほどそうした考え方があるのですね。」とは先の工場長の言葉です。
考えるためには知識が必要です。不良率が加工数と不良率を比べるのと同様に、工程能力指数はバラツキと規格幅や差、ズレを比べます。
「比べる」は状況数値化でしばしば使われる手です。品質管理だけではなく、工場経営全般で活用できる考え方です。
経営者は右腕役や現場キーパーソンに「比べる」ことを指導します。「比べる」は考えることを促すからです。そのためには比べる対象を教えなければなりません。
経営者が比べる対象を教えます。
次は貴社が挑戦する番です!
成長する現場は、不良率を卒業し、製品品質の均一性を高めて品質コストを下げる
衰退する現場は、目前の不良品や手直し品の数量を減らすことだけに満足する