「生産性ロードマップ戦略」—儲かる工場経営を目指して—第372話 現場の言動を翻訳して共通用語を整備しているか?
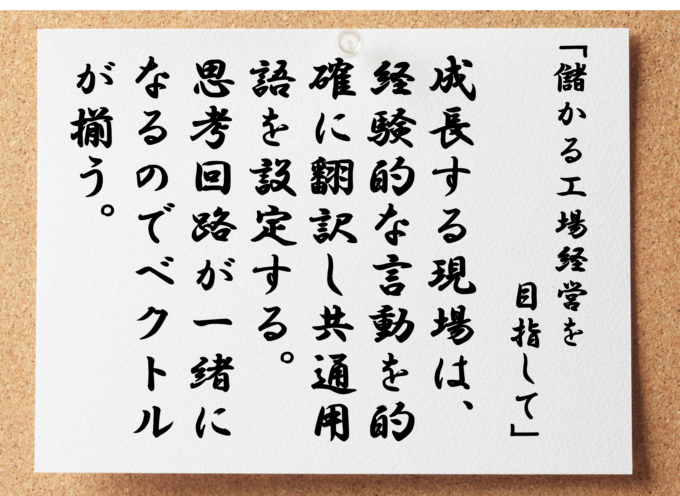
「在庫ルールをはっきりさせていなかったからですね。」
日程計画を導入しようとしている切削加工企業、工場長の言葉です。
設備に人が紐づいています。少数精鋭の中小現場でしばしばみられる属人的な職場です。仕事が職人のやり方になっています。
日程計画立案も個力依存です。
製品によって使用する設備が決まるので、結果として、製品に人が紐づきます。その製品をよく知っている作業者に日程計画を任せていました。
日程計画立案が個力依存になっていること自体に問題はありません。
製造業の従業員は一人残らず納期遵守の意識を持っています。したがって、作業者に日程計画を任せても、納期遵守は維持され、揺るぎません。
事実、その企業は、主要お客様から、納期や品質にしっかり対応してくれる優良協力会社とてしばしば評価されてきました。
ただし、その結果、我が社が儲かっているか?というと話は別です。
そうなっていないと工場長は以前から感じていました。
言い換えると、個力による部分最適化に留まっていて、チーム力による全体最適化になっていないということです。人時生産性を高める実務が進みません。
例えば、先の企業では、棚卸資産が年々、増加傾向にあるという経営問題を抱えています。売上高は横ばいにもかかわらずです。これは、事業を成長させたい経営者にとって頭の痛い問題です。工場長も材料在庫の増加が気になっています。
なぜ、材料在庫が増えているのか?
作業者一人ひとりは与えられた仕事を確実にさばいています。納期遵守で分担をこなそうとしているのです。
ただし、日程計画立案を作業者に任せていこともあって、工場長は詳細な事情で把握できていないところもありますが、材料在庫増の原因を推測はできています。
規格品生産の現場です。主要お客様から、毎週、この先3か月分製品別要求数情報が届きます。いわゆる三発内示です。
その情報が届いたとき、完成品在庫数と必要出荷数から必要製造数を決めるのが担当作業者となっています。
多くの製品を多頻度小ロットで出荷している現場です。毎日、50個出荷とか、金曜日毎に100個出荷とか、そうした製品が大部分を占めています。
したがって、この現場での日程計画ミスは欠品で現れます。
そして、担当作業者が絶対にやらかしたくないのは納期遅延や欠品です。
先の企業では、昨今、3か月分製品別要求数情報の数値変動が大きくなってきました。先週より、ぐっと増えたと思ったら、次週はガクッと減る。市場変動が大きくなっています。
そうなると、欠品したくない作業者はどうするか?
作り溜めをしようとします。欠品を避けるために、言われなくても在庫を積み上げます。そして、材料も余裕を持って購入しようとするはずです。誰も失敗はしたくありません。
会社全体の事情は知らないけれども、自分の担当では絶対に欠品したくない・・・。
個力による部分最適化がやられます。その結果が昨今の材料在庫増につながっていると、工場長は考えていました。
工場長に「在庫ルールはどうなっていますか?」と尋ねたところ、「ルールはないです。」との答え。そこで、状況を整理して要点を列記しました。
そこで工場長は気付きました。
意識しないうちに現場では安全在庫を積んでいたのです。
作業者が自分の判断で、個別に安全在庫を設定し、それでずっとやってきました。すったもんだしながらも、納期遵守ができていたので、誰も気にしていなかったようです。
お客様の変動が大きくなった結果、欠品を避けるため、在庫が増えていきました。在庫ルールが無ければ当然にそうなります。冒頭の言葉です。
そもそも、工場長には「安全在庫」という意識がありませんでした。
先の現場の作業者は、従来から、毎週届く製品別要求数情報にもとづいて、必要製造数を出してきました。そこには自然と余裕代が含まれます。安全サイドに考えたいから当然です。
この余裕代が、安全在庫に他ならないのですが、作業者自身は自分が安全在庫を設定して積み上げている意識はありません。
工場長もそれが安全在庫であるとの知識がなかったので上手く状況を説明できなかったのです。一旦分かれば、その知識を生かして全体最適を構築できます。
お客様要求数の変動に対応して欠品を回避したかったら、やることは在庫の積み上げです。日程計画の都度変更というやり方もありますが、業務が仔細にわたって煩雑になります。
煩雑な業務の代わりに、在庫を積み上げるのです。安全在庫が変動を吸収してくれます。
ただし、棚卸資産が増えます。眠ったお金が増えるので運転資金増です。経営者は気になります。安全在庫は工場経営に影響を及ぼすものです。ルールを決めます。
工場経営に影響を及ぼす事項です。作業者に決めさせるルールではありません。
経営者が安全在庫の決め方をルール化して、右腕役や現場キーパーソンへ教えるのです。知識がなければ考えられません。我流に陥ります。
安全在庫という共通用語を導入しようとしています。先の工場長は現場のベクトルが揃えやすくなりました。思考回路を同じにできるからです。共通用語になるということは、それは重要なことであると従業員へ伝えていることに他なりません。
こうやってトップダウンの指示導線が強化されていくのです。経営者は内のことを現場に任せられるようになります。
●完成品在庫の安全在庫数の決め方。
・お客様要求数のバラツキおよび製造リードタイムと製造頻度から計算する。
・在庫数ゼロ日を基準に何日分(何個分)遡って、次回完成品を積み上げるか?決める。
前者は古典的な安全在庫の計算方法です。後者は実績から判断します。理論と実績の両者を比べて適切な安全在庫数を設定するのです。
安全在庫数のルールが決まれば、全従業員の思考回路が同じになります。部分最適から全体最適への移行です。
日程計画を導入する目的は、全体最適な製造を実現することにあります。
30人規模の製造現場なら部分最適でも現場を回せるので、作業者に日程計画を任せていいかもしれません。ただし、全体最適の視点がないので、特急や突発、変更へに弱いです。
現場の主要業務にルールがないと、判断基準は各作業者になってしまいます。各作業者が判断基準となって決められるのが部分最適です。
できることしかやりません。無理をしないのが部分最適です。これでは柔軟性、機動性、小回り性という中小の強みを発揮できません。人時生産性を高める機会を失います。
全体最適がなければ、中小現場のフットワークの軽さを発揮できないのです。
人時生産性を5,000円、6,000円と増やしたいのなら、できないことをできるようにする、全体最適の視点を持った製販一体の製造に取り組まなければなりません。
お客様の特急や突発、変更へ対応するには、全体が見えている必要があります。
個力による部分最適化に留まっていた現場をチーム力による全体最適化の現場にステージアップするのです。納期遵守に加えて、儲けるための付加価値額積み上げ意識も浸透させます。
自分の分担をただこなすだけでなく、我が社が儲かるにはどうしたらいいのか?この思考回路を現場へ埋め込むのです。眠らせるお金も必要最小限にしなければなりません。
ベクトルを揃える共通用語が必要です。
在庫自体は悪ではなく、無管理の在庫が悪です。日程計画の導入には、生産管理3本柱の知識が必要になります。我流を避けるためです。考えるには知識が必要です。
「ウチも安全在庫を積み上げていたのですね。ただ、勝手にやらせていたようです。」とは先の工場長の言葉。2種類の在庫の違いを知り、現場へ的確に説明できるようになりました。現場が経験的に語っていることを正しく翻訳して我が社の共通用語にするのです。
先の工場長も長年、もやもやしていたことが、安全在庫という言葉で全てスッキリ説明できると感じています。共通用語が増えればベクトルが揃いやすくなるのです。
属人的、職人的な職場が、チームで仕事ができるように変わる一歩目を踏み出しました。
日程計画の導入では現場力が問われます。ベクトルが揃った総合力次第です。在庫管理をはじめとしたQCDに関する実務ルールが
経営者は、現場が経験的に語っていることや行動していることを正しく翻訳して我が社の共通用語にするのです。ベクトルを揃えて、儲かる工場経営の要点を浸透させます。
工場経営の本質は他人の力を借りて経営者の想いを実現することにある以上、経営者は従業員の協力を引き出さなければなりません。
ベクトルを揃える仕掛けが必要です。
●言動の翻訳→共通用語の整備→思考回路の共有→ベクトル揃え→内を現場に任せる
次は貴社が挑戦する番です!
成長する現場は、経験的な言動を的確に翻訳し共通用語による全体最適でベクトルが揃う。
衰退する現場は、属人的、職人的で作業者別の部分最適に留まるのでベクトルは揃わない。