「生産性ロードマップ戦略」—儲かる工場経営を目指して—第381話 新しい工場で何を目指すのかはっきりさせたか?
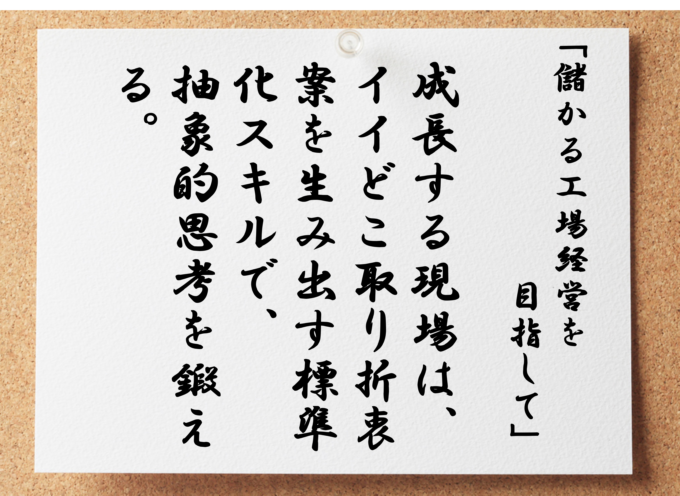
「新しい工場では高い生産性を目指したいです。」
先日、個別相談をいただいた部品メーカー経営者の言葉です。
新工場の検討に着手した経営者です。これまで必要に応じて、都度、設備を導入してきたのですが、今の工場だけでは手狭になってきました。今の工場は、継ぎ足し、継ぎ足しで拡張してきたので、場内物流に改善の余地があります。
受注環境はいい状況が続く見通しです。先の経営者はこの機会を活かして新工場を立て、成長路線を歩みたいと考えています。利益アップと給料アップを目指して人時生産性を高めるのです。冒頭の言葉です。
ただ、何から考え始めて、それを実現させるのか?
経営者には具体イメージが浮かびません。プラントレイアウトの考え方をお伝えしました。
ロジスティックの論点にデカップリングポイントがあります。儲かるモデルを考えるフレームのひとつです。
資材を調達して製造し、お客様へ納入するまでの納入リードタイムは、一般的に、お客様の希望納期に応えられません。お客様の希望納期は即納です。お客様は、欲しいと感じたらすぐ手に入れたいと考えます。
造る側は見込生産による即納体制を敷くことになります。
ただ、このやり方では、積み上げた在庫の一部が死蔵在庫になるリスクがあるのです。そもそも、見込生産ができない商品や製品もあります。そこで、実践でやられるのが見込生産と受注生産の折衷案です。
部品や中間製品を見込生産して在庫を持ちます。その後、お客様からの注文を受けてからそれらの在庫を使って最終製品の製造に着手するのです。
見込生産と受注生産の分岐点をデカップリングポイントと言います。自動車の組み立て工場のモデルはこれです。
自動車部品は見込生産、組立は受注生産であり、工程管理としては前半が引張式、後半が押出式になります。お客様の多様な仕様と短納期に応える具体策のひとつです。
見込生産と受注生産のイイどこ取りをします。
昨今のモノづくりは複雑化、高度化しています。お客様から手間暇のかかる仕様、小ロット、そして短納期の要望が届くのです。
中小製造企業は、自社の事情に関係なく、こうしたお客様の要望に応える努力をしなければ生き残れません。お客様は多数の選択肢を持っているからです。
我が社が提供できる商品、製品、サービスが「唯一、ウチしかできないモノ」なら、お客様の要望に応える努力をする必要はありません。お客様が私たちのやり方に合わせてくれます。
ただし、製造業において、唯一、ウチしかできないモノはほとんどなく、私たちには必ず、競合先があります。お客様にとっての選択肢です。
競合先より一歩でも前に出て、お客様に選んでもらう要点をつくることが中小製造企業の経営課題です。できないことをできるようにしなければなりません。
お客様の要望に合わせて、我が社を変えるのです。これが儲かる事業モデルを造る経営者の姿勢です。
「できないことをできようにする」要点のひとつが「折衷案」です。先のデカップリングポイントは一例と言えます。見込生産と受注生産のイイどこ取りです。
具体-抽象-具体の思考が試されます。
弊社ご支援先は100人以下規模の中小現場です。30~50人規模がほとんどとなっています。こうした現場で、製品別レイアウトは稀です。ほとんどが機能別レイアウトになっています。柔軟性を求めるので、これが普通です。
ただ、これだけでは、儲からなくなりました。多品種小ロットに加えて、一定水準の短納期、一定水準以上の数量にも対応できなければ、安定した収益を維持できません。
先の経営者も短納期がお客様に選ばれる要点になってきました。多品種小ロットに加えて、短納期です。これまでのやり方では競合に負けます。実際に何度も負けているのです。
したがって、新しい工場では、従来の機能別に加えて、製品別の機能も欲しくなります。
・今の機能別レイアウトの状況を整理する。(具体)
・そこに製品別を加えて、メリットを明らかにする。(抽象)
・新たな現場のレイアウトと手順を具体化する。(具体)
具体-抽象-具体の思考。仕組みづくりを担う右腕役や現場キーパーソンに持って欲しい思考法です。
しかし、この議論が進まないことがしばしばあります。製品別の流し方はウチではできないとの考えに囚われ、思考が停止するのです。
・ウチの製品は特注品なので個別生産しかやりようがない。
・ウチの製品は特注品で工程が複雑だからやりようがない。
納期遵守で目前の仕事をこなすことに一生懸命になっていれば具体的な思考が優先されます。目に見えることを具体的にさばくことが現場の仕事です。
ただ、今後、経営者が社長業に専念するために、工場を現場に任せたいのなら、右腕役や現場キーパーソンには、新たな思考のやり方も身に着けてもらわなければなりません。
これは訓練次第で高まるスキルです。
弊社がプロジェクトを通じて支援をする所以でもあります。
・具体-抽象-具体の思考で見込生産と受注生産のイイどこ取り折衷案を生み出す。
想像力を働かせ、組み合わせで価値を生み出す思考です。
これは行きつくところ「標準化」に繋がります。この「標準化」は儲かる工場で極めて大切な思考であることは言うまでもないことです。
・目前の具体的な複数事象から共通要素を引っ張りだすこと。
・共通要素に基づいて分類すること。
・そうして新たなルールをつくること。
・そして現場で守らせること。
これが標準化です。
共通要素を引っ張りだすこと、分類することは抽象的な思考になります。
訓練すれば、無意識にできることです。
先の経営者は、新しい工場で、圧倒的に高い生産性を目指したいと考えています。プラントレイアウトのお作法を使って、もれなく検討するのです。
ご支援先で、新工場立ち上げを指導するとき、必ずクリアしてもらう確認事項が20項目程度あります。これは自動車部品工場時代に実務で使用したものを中小製造企業向けに練り直したものです。
1.数量増、ライン増の拡張性、2.プロセス変更、工程追加の融通性、3.モノの流れの効果(最短リードタイム)・・・・・・。上位項目で確認するのはモノの流れです。
工程管理で言うところの手順計画となります。「見込生産と受注生産のイイどこ取り折衷案」はここで考えることになるのです。
生産性を高めるプラントレイアウトでは大手の事例も参考になります。そのコンセプトや考え方を参考にしたいです。
●大手の事例
1)アイシンのEV向け電動アスクル生産ライン
下記の2つを組み合わせて、多新種に生産性高く対応できる。
・自動化が可能で共通化できる工程は全自動無人ライン
・自動化、共通化が困難な工程は手作業有人ライン
(出典:日経ものづくり2022年11月)
2)マツダ 新しい車体生産ライン「フレキシブルモジュールライン」
車種によって変わらない部分と変わる部分に分けて、多くの車種に生産性高く対応する。
・車種によって変わらない共通部分の工程フローや工程配置は固定して変えない。
・車種によって変わる変動部分は3つのモジュール(汎用セルモジュール/治具モジュール/工程モジュール)で必要に応じて切り替え、変動部分を吸収する。
(出典:日経ものづくり2020年7月)
3)ダイキン 家庭用エアコンの組立ライン
インドでの増産を早期に実現させるために、新たなプラントレイアウトを採用する。
・生産ラインの構成を、搬送モジュールと検査モジュールの2つの設備モジュール化により素早い立ち上げを可能にする。
(出典:日経ものづくり2022年11月)
「確認事項が整理されていると全体像が見えてきますね。」とは先の経営者の言葉。お作法とはそういうものです。
お作法に「我が社ならでは」を加えて「独自性」を生みます。お作法抜きの「我が社ならでは」を「我流」と言います。
個別相談を通じて、新しい工場で何を目指すのかがはっきりとしてきました。増産のためだけの工場新設はモッタイナイです。生産性を高くして、どんな価値をお客様に提供するのか?
見込生産と受注生産のイイどこ取りはそれを実現させる方針のひとつです。
先の経営者にとっても、新たな挑戦の場は、右腕役や現場キーパーソンに抽象の思考を指導する場になりそうです。標準化スキルも身につけてもらいます。
次は貴社が挑戦する番です!!
成長する現場は、イイどこ取り折衷案を生み出す標準化スキルで抽象的思考を鍛える
衰退する現場は、具体的思考で納期遵守に頑張るが生産性を高める抽象的思考に至らない