「生産性ロードマップ戦略」—儲かる工場経営を目指して—第388話 情報でモノの流れを管理しているか?
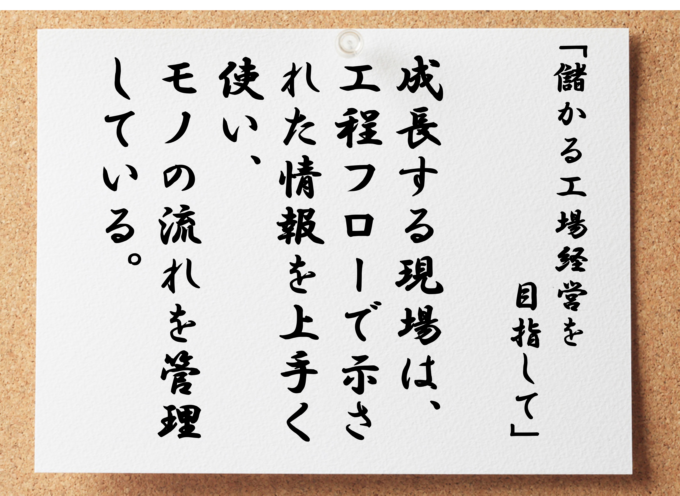
「全体の流れが見えてきました。」
30人規模紙加工企業幹部の言葉です。
その幹部は、納期遅れが発生すること、納期回答に時間がかかることを改善しようと考えています。今の主要なお客様にご迷惑をかけているからです。主要なお客様との関係が良好なうちに解決しなければなりません。
目標は日程計画の導入です。ただ、日程計画を検討する前にやるべきことがあります。モノの流れの整理です。
現場キーパーソンへ「我が社のモノの流れ」を尋ねると、回答がまちまちでした。
各現場キーパーソンは各自に任されている工程のことは、(当然)分かります。ただ、その他の工程は「なんとなく」になっているのです。
つまり、モノの流れ全体を的確に説明できる現場キーパーソンが居ません。この状況で日程計画を導入したら、どうなってしまうかは明らかです。
生産管理3本柱のお作法から始めました。手順を伝えて、整理をしています。
冒頭の言葉です。
工場には2つの流れがあります。
情報とモノです。
経営者はモノの流れを情報でコントロールします。
経営者が従業員と一緒になって現場でモノをコントロールしていては儲かりません。経営者の仕事場は外にあるからです。
経営者に代わってモノの流れを管理するのが右腕役の役割です。
右腕役は、まず情報を集めます。
日程計画や生産進捗、仕掛品や完成品の在庫数推移などが具体情報です。したがって、必要な情報が右腕役に集まる仕組みが必要です。
情報の流れを作るのは発信者と受信者です。情報は従業員と従業員の間を細かく繋いで右腕役に届けられます。そこを仕組み化するのです。
そうしないと安定した情報の流れができません。右腕役は「情報収集」という余計な仕事をする羽目に陥ります。
この仕組みができてはじめて経営者は右腕役と一緒にモノの流れを情報でコントロールできるのです。
情報が流れる仕組みをつくらないと、右腕役は情報を収集することに時間を割かれ、活かすまでに至りません。情報は活かしてなんぼです
経営者は情報でモノの流れをコントロールします。最適なモノの流れを設定しなければ儲からないのです。そのモノの流れを設計するのが工程フローです。
工程フローは工程管理の手順計画に相当します。これはプラントレイアウト検討の初期段階で決定されるフローです。「工程数」はここで決められます。工程フローを見れば、モノの流れが一目でわかります。
リードタイムは原則、工程毎に計算されるものです。また工程数は少なければ少ないほどリードタイム短縮にも貢献します。工程数は重要項目です。そこで、先の企業では工程フローを見直しました。
工程毎リードタイムは標準時間(製造数量に比例する時間)×製造数量+標準時間(製造数量に関わらず一定な時間)で計算されます。第二項の代表的な項目は段取りです。
工程数によって、標準時間の「構成」が変わります。そして、進捗管理は工程毎です。工程毎に管理業務をやります。
さらに工程数で工程間数が決まります。そして、その工程間には運搬-停滞-運搬という価値を生み出さない工程が現れるのです。
先の現場では、各工程の定義が曖昧でした。なんとなく、生産の流れを「複数工程の塊」でとらえていたのです。これでは、リードタイム計算も管理も曖昧になります。
そこで、モノの流れを独立した工程で定義し直し、整理しました。管理しやすくなります。モノの流れを決めるとき、「工程数」は重要項目です。
さらに工程フローで明らかにされる重要項目に「単線、複線」があります。
扱っている製品が単品なら単線、組立品なら複線です。単品は外注先も含めて、内製工程を繋いでいけばできあがります。
一方、組立品は本線に各種部品が合流する複線です。合流ポイントは流れの制約になります。本線が進んでも、合流してくる分が遅れたら、待たないとなりません。合流点はモノの流れをコントロールするとき要点となります。
先の現場にも合流点がありました。
「なるほど、ここをおさえれば流れがスムーズなりそうです。」
工程フローを手にしながら語った先の幹部の言葉です。
工程フローを手にできれば種々のことが見えてきます。見えれば説明できます。説明できれば右腕役に内を任せられるのです。
現物を扱っている以上、モノの流れは現場と一緒に理解されていないとなりません。現物は大きさがあり重さもあります。スムーズな流れを作らないと扱いが大変です。
現物の扱いは工程フローに従います。大きさがあり、重さもある「現物」を扱っているので、工程フローを整理するのは重要な仕事なのです。
製造業のモデルにファブレスがあります。現物を扱いません。一方、私たち中小製造企業のほとんどは、現物を扱っています。ファブレスと相対するモデルです。
ファブレスは儲かるモデルと言われます。現物を扱わないので、その分の工数を全て、企画、開発、設計や販売、アフターサービスへ割けるのです。儲かる所以がここにあります。
私達は、“あえて”現物を扱っています。
“あえて”現物を扱っているのはなぜか?
これは意外と重要な問いかけです。
工程フローで流れが見えた先の幹部は工程表に取り掛かろうとしています。これまで経験と口頭だけでやっていた仕事を、今後は、工程表を通じてやりたいと考えています。
標準時間を算出するためです。さらには工場間をまたぐモノの流れもあります。その点も明らかにする必要もありそうです。
「工程図もやった方がいいですね。」
先の幹部は工程管理を右腕役に意志と意図を伝える道具として使い始めています。
これまでは、問題が起きてから手を打つ現場でした。これからは情報を通じて、先手を打って、淡々と、モノの流れを管理する現場に変えていきたいと先の幹部は考えています。
まずは幹部や現場キーパーソンのベクトル揃えが必要です。工程フロー、工程表、工程図はベクトル揃えのための「共通認識」「共通用語」をつくるのにも貢献します。
利益アップ、給料アップの人時生産性は付加価値額を「積み上げる」です。お客様の要望に応えるために、できないことをできるようにしなければなりません。チーム力が問われるPJです。メンバー間で「共通認識」「共通用語」を持つことがPJの成功要因となります。
次は貴社が挑戦する番です。
成長する現場は、工程フローで示された情報を上手く使い、モノの流れを管理している
衰退する現場は、経験と口頭だけでモノの流れを管理しようとして、すったもんだが起きる