「生産性ロードマップ戦略」—儲かる工場経営を目指して—第410話 多品種少量現場を「分類」の視点で見ているか?
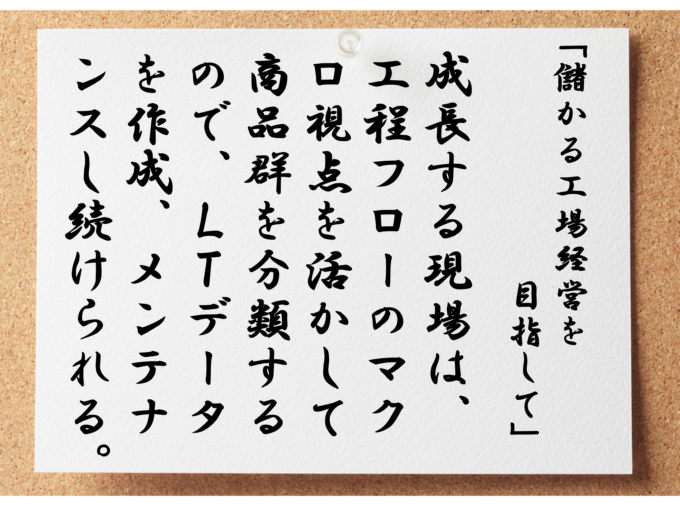
「ウチは多品種なのでマスターデータ作成が煩雑になりそうです。」
プロジェクトに着手して数か月経過した製造担当幹部の言葉です。
日程計画は従来からありますが機能していません。なぜ機能していないのか?日程計画に必要なリードタイム(LT)のマスターデータがないからです。
マスターデータがないので、日程計画立案の判断基準は”売上高規模感”にもとづく幹部の勘と経験になっています。実際の所要時間と大きなずれが生じるのです。
結果として、工番全体が遅れ気味になっています。製造納期を遵守できない事態にたびたび陥っている現場です。
そうなると、現場では、納期に遅れそうな工番の火消しに追われるだけです。この状況から抜け出したい経営者は現場改革を決意しました。
改革の初手は日程計画と進捗管理の仕組みづくりです。リードタイム(LT)を定義してマスターデータを整備します。ここでは標準化のスキルや考え方が問われるのです。
先の幹部にとって、標準化の実務は初めです。多品種の商品リストを前にして、標準化ができるのだろうか?との懸念が浮かんできました。
冒頭の言葉です。
製造業に限らず商売の基本はお客様の要望に応えることです。要望のひとつに納期遵守があります。これは商売の基本です。納期を守れないメーカーは選ばれません。納期遵守は大事です。ただ、昨今、お客様の納期に合わせて造るだけでは儲からなくなってきました。
原材料や運賃、費用高騰のあおりを受けて付加価値額率が悪化、儲けが出にくい状況に直面しているご支援先も少なくありません。
どうするか?
お客様の納期ではなく、我が社が儲かる納期でドンドン仕事をさばき、付加価値額を積み上げるのです。
詰めて、空けて、取り込む、リードタイム短縮。製販一体総力戦で苦境を乗り切ります。先の現場で構築したい体制です。
我が社が儲かる納期はお客様の要望にも応えていることになります。
「詰めて、空けて」を実践するには、リードタイム(LT)のビフォーアフターの設定が欠かせません。我々の作業時間は今、どれくらいなのか?標準作業時間があって初めて、詰める目標が明らかにされます。先の企業にはこれがないのです。
標準作業時間が無いので、日程計画は勘と経験に基づくことになり、「詰める」以前の状況に陥ります。日々、明日、明後日、3日後に出荷する工番の遅れを確認して、遅れを認識したら挽回をするしかありません。
先の現場では標準作業時間が設定されてなく、計画の精度が低いため、納期を守るだけで手一杯です。リードタイム短縮どころではありません。挽回がやっとです。
リードタイムのビフォーがなければ、こうなります。
・標準がなければ、日程計画の精度が低くなるから納期を守ることで手一杯になる。
・標準があれば、リードタイムのビフォーアフターでリードタイム短縮に取り組める。
リードタイムを定義して、標準の工程リードタイムと製造リードタイムを設定すれば、ビフォーを設定できます。ここで、初めて「詰める」ためのアフターが明らかになるのです。
標準作業時間、マスターデータなしのリードタイム短縮はあり得ません。
作業時間の標準化作業、マスターデータ作成では、工程毎リードタイムを計測して整理します。ここは地道にやるしかありません。
ただし、ここでやるべき重要なことがあります。
・商品、製品を群やグループで分類
多品種少量の我が社の商品、製品を群やグループで分類します。闇雲に計測をしません。標準化のスキルや考え方が問われるところです。
なぜ商品、製品を群やグループで分類することが必要なのか?
マスターデータ作成、標準化で推測や推定をできるようにするためです。これが標準化の体系となります。
マスターデータは作られたら、それで終わりではありません。精度を維持、高めるメンテナンスが大事です。
その際、各マスターデータが個々に独立して存在している場合、整備はデータ個々にやらなければなりません。手間が掛かります。
一方、グルーピングができていれば、そのグループを特徴づける要因に注目できます。その要因を活かして推測、推定ができるのです。実測に比べれば精度は落ちるかもしれません。
ただし、ここで、日程計画のマスターデータで求められる精度に関して、思い出したいことがあります。
・データに求められる精度は日程計画を機能させる水準で十分であること
小日程計画の時間単位を考えればわかることです。
マスターデータに求められる精度の水準を知っていれば、推測、推定を使いたくなります。
マスターデータの精度水準は、日程計画の時間単位で決定されます。その時間単位を満たせば十分なのです。貴社の時間単位はどれくらいですか?
そして、上手い分類はデータ作成やメンテナンス楽にしてくれます。
同一分類内では、特徴づける要因があるので、工程リードタイムや製造リードタイムの推測、推定はし易くなるのです。
マスターデータ分類の観点が大事です。
マスターデータ分類のやり方を教えてくれるのは「工程フロー」「プロセスフロー」です。
工程管理の2本柱のひとつ生産計画。
その中に「手順計画」があります。
そして、ここで使われる3点セットのひとつが工程フローです。
モノの流れを明示した工程フローは、プラントレイアウト検討において、初期段階で設定されます。これが決まらないとその後の工場レイアウトを明らかにできないからです。それだけ重要と言えます。
この工程フローに紐付いて整理されるのが工程表と工程図です。
・工程フロー - 工程図 - 工程表
この3点セットでモノ流れを規定します。そして、3点セットの最上位にある工程フローが分類のやり方を示してくれるのです。
工程フローで規定しているのは次の2項目。
・工程数
・工程順序
この2つがモノの流れの土台を決めます。したがって、工程数と工程順序がモノの流れの特性を決めるのです。これらで分類します。
工程フローが同一ならば、モノの流れの特性が同じです。リードタイムは推測、推定しやすくなります。
同一分類内での工程リードタイムや製造リードタイムのデータ作成やメンテナンスは楽になるのです。実務をやれば、このことを肌感覚で理解できます。
「細かい作業では差異がありますが、同じ分類にしていいでしょうか?」
商品リストを作成した後の幹部の言葉です。
我が社は多品種少量であるとの思いが強すぎると、視点が商品毎の作業内容の差に向いてしまうようです。
商品毎の作業内容差を認識することは管理上、大事ですが、ここでの趣旨はリードタイムを設定しやすくすることです。求められるのはミクロ視点ではなく、マクロ視点と言えます。
・データに求められる精度は日程計画を機能させる水準で十分であること
これを思い出せば、自ずと答えが出ます。
こうした考え方はいわゆる工程管理でのお作法です。さっさと現場に習得させて実務を進めさせたいところです。
日程計画と進捗管理の仕組みづくりの本質は、こんなお作法にはありません。設定したマスターデータと実績との摺り合わせにあります。
早く、その段階へ至りたいのです。
先の幹部も理解した考え方をプロジェクトメンバーと現場キーパーソンへ説明し始めました。お作法はさっさと身につけるべきです。
我流でない共通用語を醸成するための思考回路が埋め込められます。
当初は煩雑になると考えていたマスターデータ作成が「分類」の観点を導入することで見通しがよくなりました。後は、日程計画立案で使うリードタイムを計算するプログラムをつくればいいだけです。その後、データと実績の摺り合わせを始めます。
多品種少量の現場ではしばしば「分類」の思考回路が求められます。
分類=標準化です。
次は貴社の番です!!
成長する現場は、工程フローのマクロ視点で商品群を分類しLTデータを整備し続ける。
衰退する現場は、商品群を分類せず闇雲にLTデータを整備するうちに疲れて続かなくなる。