「生産性ロードマップ戦略」—儲かる工場経営を目指して—第413話 現場キーパーソンの業務負荷を把握しているか?
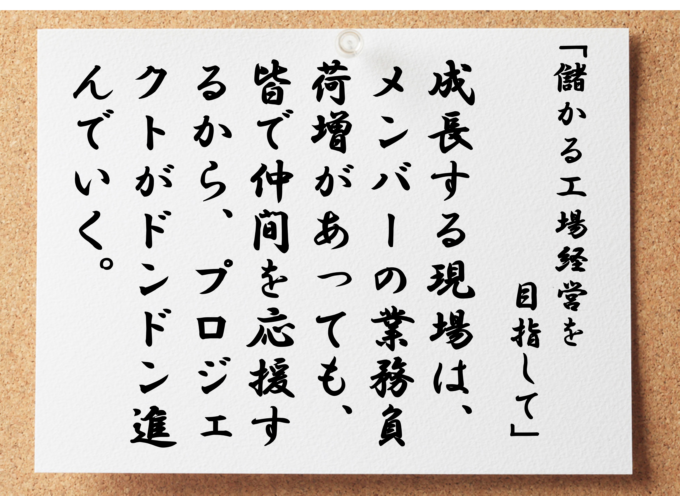
「先生、現場での作業が半分以上あります。」
PJ事前打ち合わせでの自動車部品メーカー現場キーパーソンの言葉です。
プロジェクトメンバーとして3名現場キーパーソンが選ばれました。PJの実務担当として現場を引っ張ります。
従来業務にPJ業務が加わり負荷が高まりますが、そんなことは意に介さない若手です。頼もしい人材です。
これから人時生産性向上PJの実務にとりかかるわけですが、まずは、今の仕事ぶりを確認します。「指示や指導する管理者業務の他にやらなければならない仕事はありますか?」との問いに一人の現場キーパーソンが答えてくれました。
冒頭の言葉です。
他のメンバーも同じ状況に直面しています。納期遅れ対応や突発の欠員補填のため、現場作業に従事せざるを得ないことがしばしばです。
就業時間8時間のうち、現場に4~5時間、入らざるを得ないこともあります。
人時生産性を高めるには手順があります。基本のフレームは「外と内」です。
製造業とは市場と向き合って外部の変化へ対応する事業なので、社長の仕事場は外にあります。そして、その外の変化に合わせて、内を変えるのが、製造業での仕事のやり方です。
現状維持は相対的な後退になります。技術も競合もドンドン前へ進んでいるからです。
人時生産性向上PJとは意識改革、現場改革、構造改革、変える活動に他なりません。
改革のゴールは構造改革です。儲かる事業モデルを創り上げます。儲かるか儲からないかは全てこのモデル次第です。改革と改善の違いはここにあります。
改革はモデルづくりです。これは経営者の仕事です。
儲かる工場経営の要諦は「お客様に選ばれる商品を効率よく造ることにある」です。したがって、製造業の事業モデルは「商品」で決まります。
どうやって造るか?の前に、何を造るかです。儲けるにはこちらの方が大事です。
繰り返しますが、経営者の仕事場は「外」にあります。
そうして、その後、「効率よく造る」に焦点を当てるのです。せっかくお客様に選ばれた商品なのに、効率低く造っていては儲かりません。
効率を高め、詰めて、空ければ、仕事を獲り込めるので儲かります。効率を高め、詰めて、空ける実務は現場の仕事です。
リードタイム短縮のタームマネジメントをやります。工程間連携がカギです。横のつながり、横の連携とも言います。
切断→プレス→曲げ→塗装→組立→検査→梱包
製造工程は複数で構成されます。現場ではモノを「仕掛品」として工程間で受け渡していくのです。工程内連携、工程間連携が機能していないと上手くいきません。
この横の連携がないと、商品や製品を効率よく造れなくなりました。高度化、複雑化している製造業では、チーム力が求められる所以です。
現場での工程内連携と工程間連携は作業者一人ひとりの思考回路に依存せざるを得ません。
作業者が仕事をしていて、手にしたワークに不具合を見つけたとき、その作業者は適切な対応をしてくれるかどうか?
これは、作業者の頭に経営者の顔が浮かぶか浮かばないか、それ次第です。
経営者が日頃から、「作業者の頭に経営者の顔が浮かぶ」につながる言動をしていれば、手間暇が掛かっても、その作業者は適切な対応をするでしょう。
そうでなければ、その作業者は、自分勝手な判断基準で対応することになります。
工程内連携と工程間連携は、一人ひとりの思考回路に依存せざるを得ないのです。
経営者が現場に張り付いて、ずっと、直接指導できるなら、間違いは起きません。しかし、経営者の仕事場は「外」にあります。工場を不在にしなければ、市場と向き合えないのです。
経営者が不在でも、現場で「工程内連携」と「工程間連携」を機能させるには、作業者一人ひとりの思考回路に「工程内連携」と「工程間連携」を埋め込むしかありません。
作業者一人ひとりの思考回路に工程内連携と工程間連携を埋め込んで、横のつながりをはたらかせるのに必要なのが4階層の指示導線です。
厳密なトップダウンで横連携の思考回路をつくります。工程間連携を実現したかったら、厳格なトップダウンです。そのトップダウンを4階層でやります。
指示導線によるトップダウンを機能させる要点は、上から2番目と3番目にあります
管理する人と指示する人。
本来、切り分けて分担したいところですが、少数精鋭の中小現場では両者を一人の現場キーパーソンが担うこともしばしばです。管理もするけど、現場への作業指示もやる。
先の3名の現場キーパーソンは皆、こうした状況に置かれています。
管理業務では仕組みづくりとフィードバックがあり、指示業務では作業者1人ひとりへ目配せするフォローと評価があるのです。同時並行でやるには、少々負荷が高くなります。
大手でこの2つを一人でやることはありません。そもそも、数百人規模の現場ではそうできないのです。管理業務を担うスタッフ(間接業務員)がいます。
先の3名の現場キーパーソンは、皆、管理と指示の両方に担っていることに加えて、作業もやっているのです。
それも、場合によっては半分以上の工数が割かれます。ここに納期遅延、品質クレーム、労災などの問題が起きたらどうなるかは火を見るよりも明らかです。
腰を据えた根本的対策を打つことができません。いきおい、対処療法的対策に留まることが多いでしょう。現場キーパーソンがこうした状況に置かれていることそれ自体が問題です。
こうした状況のままでPJを始めると、経営者が白羽の矢を立てた志ある若手が疲弊する恐れがあります。注意しなければなりません。
効率よく造るには、現場における横のつながり、工程間連携が欠かせません。そして、この横のつながりを強化するには、指示導線によるトップダウンが必要になってきます。
横のつながり強化は、作業者の思考回路依存なので、直接に指導したくても、上手くいかないのです。
トップダウンの環境下で醸成させます。したがって、経営者は重要な2階層分の人材の指導と育成もやらないとなりません。工場を不在にしても、指示導線を機能させるためです。
少数精鋭の中小現場が直面している状況を踏まえると、この指示導線を機能させるに、経営者がやらなければならないことがあります。
指示導線の中核を担い、PJメンバーとして現場を引っ張る役割を果たす現場キーパーソンのための環境整備です。
現場キーパーソンには、じっくり腰を据えて考え、試行錯誤し、失敗しながら経験を積んで、我が社にとって最適な改革手段を導いて欲しいのです。
片手間ではできません。そうした仕事に没頭できる環境整備です。
人時生産性向上PJは将来を見据えた取り組みです。
その取り組みは「今の仕事」と兼務できません。「今の仕事」があると、どうしてもそちらへ引っ張られます。
大手の研究開発部門が、なぜ工場とは別のところに、わざわざ建屋をつくって研究所や研究センターという組織で活動しているのか?この背景を考えれば分かるのではないでしょうか?
PJを始めるに当たって、まずは、現場キーパーソンの仕事ぶりを確認します。
現場作業に時間が割かれているなら、それへの対応は必要です。対応せずに、メンバーの裁量でなんとか乗り切ってもらうことを期待しても、限界が見えてきます。
・現場作業に時間を割かれるのは納期遵守のためなので、そちらの業務が優先される。
・一人で頑張る現場キーパーソンが空回りをして、徐々に疲弊する。
肝心のPJが前へ進まなくなるのです。
経営者は、現場キーパーソンのために現場作業に割かれる時間を最小限にする環境を整えてあげるのです。
ただ、ここは難しいです。そもそも、中小現場は少数精鋭なので、そうなっているわけで、簡単に解決できません。しかし、志ある現場キーパーソンを疲弊させたくありません。
現場作業者スキルの底上げをして、現場キーパーソンの作業負荷を減らしたいわけですが、そもそも、「スキルを底上げ」をすることがPJの目的でもあります。鶏と卵のような話です。どちらが先でどちらが後という考え方では上手くやれません。。
経営資源に制約がある中小製造現場です。
ないもののねだりをしても問題は解決できないので、経営者はそうした事態にあることを従業員へ説明し、メンバーへの協力をお願いするしかありません。全社一丸、製販一体、ここから活動を始めるので、「メンバーへの協力を頼む」と宣言します。
少数精鋭の中小現場は大手のように人材が余っていません。
したがって、足りないことは皆で補い合うしかないのです。あるいは、何かを捨てることも必要かもしれません。そうしないと、新たなことができないです。
まずは、現場キーパーソンの業務負荷を把握します。
避けたい事は孤軍奮闘する頑張る若手を放置しておくことです。「頑張ることは損をすること」という思考回路を絶対に生み出してはいけません。
先の現場では、経営者が全従業員へ宣言をしました。さらに、PJを進めるに当たってメンバーには、「一人では絶対に抱え込まないこと。助けてくださいと気軽に言うこと。」を繰り返し伝えています。
メンバーの業務負荷増は避けられません。ただ、そうであっても、周りの仲間が応援してくれると分かれば、頑張ってくれるのが志を持っている人材です。
本物の人材とはそういうものです。
そうして、仕組みができあがり、1年、2年、3年と経過するうちに気が付くと「普通にできるようになった。」となります。
仕組みづくりに特効薬はありません。地道にお作法にしたがって造るだけです。
次は貴社が挑戦する番です!
成長する現場は、メンバーの業務負荷増があっても、皆で仲間を応援するから乗り切れる
衰退する現場は、頑張る若手を放置しているので「頑張ることは損をすること」と考える