「生産性ロードマップ戦略」—儲かる工場経営を目指して—第419話 メンバーのベクトルを揃える魔法の図を使っているか?
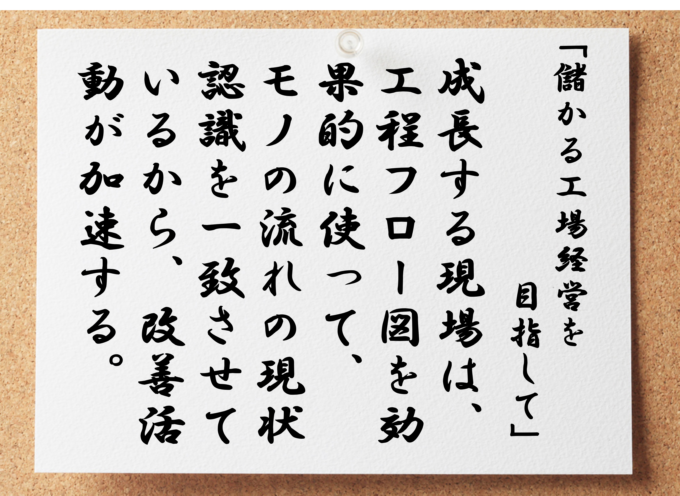
「後工程の状況が見える化でわかりました。」
これは、現場の前工程を担当しているベテラン社員の言葉です。
この企業の収益は数年にわたり低迷しています。経営者は、現場での業務効率を向上させるためには、抜本的な変革が必要だと考えています。
そこで、受注判断や日々の作業指示の方法を大きく見直す方針を打ち出しました。新たな日程計画と進捗管理の仕組みを構築するため、経営者の右腕役と現場キーパーソンを含む6名で議論を開始しました。
まずはモノの流れを整理することからです。
現場で実際の流れを確認した後、会社のモノの流れを「見える化」しました。その結果、前工程を担当するベテラン社員が整理された表を見て、新たな気づきを得たのです。
それが冒頭の言葉に繋がります。
製造現場での成果はモノの流れ次第です。多品種少量生産であろうと、効率よく製造しなければ中小製造企業は生き残れません。
お客様の要望に応えるためには、細かく繋ぎ、テキパキ切り替える、「切れ」のある現場が求められます。工程内および工程間のモノの流れをスムーズにする仕組みが必要です。
これが日程計画と進捗管理です。
その仕組みを構築する際、工程フロー図が重要な役割を果たします。
メンバーで議論する際、このフロー図を用いることで、モノの流れを視覚化し、全員が同じ認識を持つことができるのです。工程フロー図を活用することで、効率的な製造プロセスを確立し、成果を上げることができます。
QMSを構築している現場では、プロジェクト(PJ)着手時点で「工程フロー図」が存在することが多いです。しかし、こうした現場でも新たな工程フロー図を作成することがあります。
なぜでしょうか?
QMSの審査では品質が重視されます。品質不具合が発生した場合、継続的な改善活動で品質を向上させます。
そのため、品質確認に重点を置いた工程フロー図が作成されます。品質不具合品を流出させないためです。これはQMSでの役割を果たしており、正しいアプローチです。
しかし、人時生産性向上を目指す仕組みづくりでは、目的が異なる工程フロー図が求められます。モノの流れとQCDの関連を明らかにしたいのです。
具体的には、以下の論点が重要です。
・我が社の工程はいくつあるのか?
工程フロー図で工程数を明確にする必要があります。工程数が決まれば、工程と工程の間の数も決まるのです。
人時生産性向上の観点では、工程の数および工程と工程の間の数を知りたいのです。
そのためには「工程」を定義しなければなりません。ここが大事なポイントです。工程をどのように定義するのかにはお作法がありますが、最終的には現場独自のものになります。
設備レイアウトに従った見えたままの工程認識からスタートして、工程定義の論点を深めるのです。
ご支援先で議論する際の観点は2つあります。
・リードタイムを構成する項目は何か?
・品質に影響を及ぼす作業項目は何か?
まず、設備の並びに沿って、見えたままに工程を書き並べ、これら2つの観点で定義を深めていきます。
1.リードタイムを構成する項目
リードタイムを構成する項目を見極める際、段取りも独立した工程として扱います。多品種小ロット生産では、細かく繋ぎ、迅速に切り替えることが求められます。段取りの重要性は言うまでもなく、これを一つの工程として扱うのです。
また、正味作業と非価値作業を区分することも大切です。段取りは非価値時間に区分されます。工程管理で定義される工程は「加工」「検査」「運搬」「停滞」の4つです。
運搬作業も必要なら工程として扱います。中間製品や仕掛品の滞留や放置が常態化していれば、それも工程として無視できません。これらは時間を浪費する要因です。
2.品質に影響を及ぼす作業項目
品質に影響を及ぼす作業項目は、品質造り込みの観点から見直します。現場では品質不具合を防ぐために多くの工夫がされています。これらを整理して工程として扱います。
製造条件調整作業がリードタイムに影響を与えるなら、これも工程と考える必要があるかもしれません。
設備の稼働を停止して行われる製造条件調整はリードタイムに影響するのです。品質とリードタイムに影響を与える作業は無視できない工程として扱います。
この製造条件調整では「ジャッジ(判断)」が必要です。その「ジャッジ」の判断基準は数値化された形式知の場合もあれば、経験に基づく暗黙知の場合もあります。
工程フロー図に整理することで、ノウハウの蓄積が可能になり、問題を予防するための体系的なアプローチが取れます。これにより、モグラ叩き式の対応から脱却し、ノウハウ蓄積式の効率的な現場管理が可能になります。
1)リードタイムを構成する項目は?
2)品質に影響を及ぼす作業項目は?
この2つの観点で整理した工程フロー図を用いることで、メンバー全員が同じ現状認識を持つことができます。認識が一致していないと、ビフォーアフターの改善案を議論したいのに、現状確認に多くの時間を割いてしまい、非常に効率が悪いのです。
先の前工程を担当しているベテラン社員は入社して20年、前工程一筋です。そのため、後工程の仕上げ、検査、梱包、出荷の要点を、今回作成した新たな「工程フロー図」で初めて知りました。
そうした工程の存在は当然、知っていますが、鳥の目で俯瞰できたので、新たな気付きがあったのです。蟻の目では見えないことが、「工程フロー図」によって手にできた鳥の目で見えてきました。
こうした新たな発見を、素直に「なるほど」と感じられる現場には、チーム力が備わっています。そうした現場には、製造チームの凝集性に欠かせない応受援性や相互補完性を感じるのです。
全員が工程の要点を共通認識できれば、PJの進行が加速します。適切な内容が記述された工程フロー図は、メンバーの認識やベクトルを揃える「魔法の図」と言えるのです。
「現場に鳥の目を持ってもらうこと」は、経営者が外で社長業に専念するために欠かせない論点となります。蟻の目しかもっていない右腕役や現場キーパーソンに内の仕事を任せるのは少々、不安です。
このPJでは、日程計画と進捗管理の仕組みづくりを中心に進める予定でしたが、現在は品質安定化対策も加えることにしています。
先の現場の製造プロセスでは金型を使っています。金型を使用する現場では、品質安定化が特に重要です。特に相変態を伴う金型を使った加工は、品質が不安定になりやすいという問題があります。
この相変態を伴う金型を使ったプロセスは、総合芸術のようなもので、多くの制御要因や変動要因があります。そのため、品質不具合が発生した際に原因を特定するのが難しいことが多いのです。
この現場でも同じ問題があるとの声が上がってきました。工程管理担当の現場キーパーソンは、品質が安定しないために、積極的な対応ができないと説明してくれました。経営者と現場の認識に若干の差がありましたが、これを機に一致させることができます。
日程計画と進捗管理を現場に定着させるためには、品質安定化が前提条件です。経営者は、この点を仕組みづくりの際に、現場と確認する必要があります。
したがって、品質状況を把握するための品質指標の設定も重要です。品質安定化を確立することで、日程計画と進捗管理が効果的に機能し、全体の効率が向上します。
次は貴社の番です!
成長する現場は、工程フロー図でモノの流れを共有できているから改善活動が加速する。
衰退する現場は、モノの流れが共有できていないので改善の議論が進まない。