「生産性ロードマップ戦略」—儲かる工場経営を目指して—第424話 現場の数値でマクロとミクロを評価しているか?
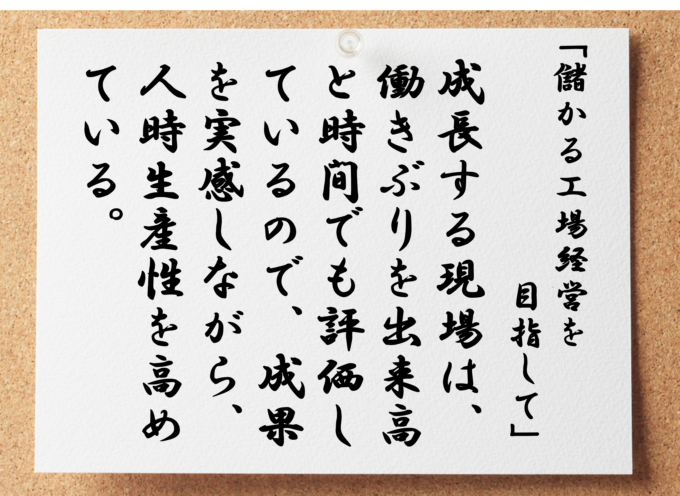
「こんなに数値が低いとは思わなかったです。」
プロジェクトに着手して数か月が経過した、設備部品メーカー工場長の言葉です。
現在、人時生産性は3,000円台後半で低迷しており、早急に4,000円台へ引き上げる必要があります。
これを達成するために、製販一体となって、現場改革に取り組む必要があります。チームの結束を強化するためには、明確な目標数値の設定が重要です。
現場の働きぶりを評価する指標には様々なものがありますが、設備総合効率はしばしば用いられます。これは設備に焦点を当てた指標で、工場全体の効率や現場の働きぶりを3つの要因で評価します。
しかし、その結果として得られる数値が予想以上に低いことがあるのです。冒頭の工場長の驚きの言葉につながりました。
人時生産性は金額で表され、儲かる工場経営では重要な指標です。
ただし、現場ではその金額が実感しにくいことがあります。なぜなら、現場では実際の作業や物の管理に重点を置いているため、成果は出来高と時間で評価されるからです。
現場は金額に対する感覚が薄いのはしかたがありません。
経営者の右腕であれば、年商や利益の規模感を把握しているでしょう。しかし、現場のキーパーソンがこれらの規模感を理解している例は稀です。
もちろん、現場のキーパーソンも経営指標を理解することが望ましいですが、現場では日々の納期遵守が最優先です。
製造業における収益構造は、固定費VS付加価値額です。
事業を成長させるためには、売上高、特に付加価値額や粗利を積み上げることが求められます。人や設備に投資をし、それを回収するというのが製造業でのやり方です。
率(利益率)よりも規模が重要であり、現場の役割は生産能力を高め、販売数量を増やすことにあります。
したがって、現場の働きぶりは出来高と時間で評価することが最も適切です。
現場のスタッフが気にするのは、自分たちの作業がどれだけの成果を生み出したかという点であり、その評価基準を明確に伝えることで、現場のモチベーションを高められます。
現場の働きぶりを評価する際、よく用いられる指標の一つが設備総合効率(OEE: Overall Equipment Effectiveness)です。
OEEは、公益社団法人日本プラントメンテナンス協会によって開発されたもので、製造現場における効率を数値で評価するツールです。
もともとはプラント向けに設計された指標となりますが、製品別レイアウトの自動化ラインや、さらには機能別レイアウトの工場でも適用できます。
この指標は「出来高」と「時間」の両方を考慮した、包括的な評価方法を提供します。
設備総合効率は、以下の3つの要因で構成されています。
・時間稼働率
・性能稼働率
・良品率
この3つの要因を掛け合わせることで、工場全体の効率を一つの数値として表すことができます。それぞれの要因を詳しく見ていきましょう。
- 時間稼働率
時間稼働率 = 稼働時間 ÷ 負荷時間
時間稼働率は、工場が稼働する予定の時間に対して、実際に稼働した時間の割合を示します。たとえば、1日の稼働予定時間が8時間で、そのうち6時間しか実際に稼働していない場合、時間稼働率は75%となります。
この指標からは、機械の故障や段取り替えなどの「停止ロス時間」がどれだけ発生しているかがわかります。
現場の日々の作業報告書(作業日報)からも確認できる、分かりやすい指標です。
- 性能稼働率
性能稼働率 = 正味稼働時間 ÷ 稼働時間
性能稼働率は、機械が実際に稼働している時間中、どれだけ効率的に作業を行っているかを示します。ここで重要なのは、「正味稼働時間」です。
これは、機械が故障なく動いている時間のうち、「性能ロス時間」を差し引いた時間を指します。性能ロスには、チョコ停(短時間の停止)や、設備の速度低下、作業者のミスによるバラツキなどが含まれます。
これらは一見すると小さなロスですが、積み重なると大きな影響を及ぼします。この性能稼働率を把握することで、現場が効率的に作業を進めているかどうかを判断できます。
「性能ロス時間」は作業者が認識し難い時間です。そこで、実務では、「出来高」で認識されます。標準加工数量と実績加工数量です。
性能稼働率は、標準加工数量と実績加工数量を比較して評価されるため、目に見える形で性能ロス時間を把握できます。
分子が実績加工数量、分母が標準加工数量です。標準加工数量は、標準時間から算出されます。管理者が期待している出来高です。
- 良品率
良品率 = 価値稼働時間 ÷ 正味稼働時間
良品率は、製造された製品のうち、どれだけが不良品や手直し品を除いた「良品」であるかを示す指標です。
ここで「価値稼働時間」とは、不良品や手直し品を作るのに費やした時間を除いた、価値を生み出すための時間を指します。
たとえば、8時間の正味稼働時間のうち、1時間が不良品の製造に使われた場合、良品率は87.5%となります。
このように、不良品や手直し品が少なければ少ないほど、良品率は高くなります。良品率は、現場の品質管理の状況を反映しており、製品の品質向上が直接的に企業の利益に貢献することを示しています。
良品率も実務では「出来高」で認識されます。
設備総合効率は時間稼働率×性能稼働率×良品率なので、負荷時間に占める価値稼働時間となります。つまり、設備を稼働させようと計画した時間のうちでお客様に届ける製品を生産するのに貢献した時間の割合です。
つまり、儲けに貢献した度合いを時間の観点で評価しています。設備総合効率は単に設備の効率を測るだけでなく、工場全体のパフォーマンスを評価する「マクロ視点」でのツールとしても機能するのです。
時間稼働率は、計画された稼働時間のうち、実際に設備が稼働していた時間の割合を示します。これは多くの現場で「稼働率」として扱われています。
性能稼働率は、標準的なリードタイムやサイクルタイムと実際の実績を比較することで算出されます。
良品率は、生産された製品のうち、基準を満たす良品の割合を示し、品質の指標として広く利用されています。
「ミクロの視点」では、これらが個別にチェックされるのです。
これらの3要素を掛け合わせて設備総合効率が算出されます。
例えば、時間稼働率が80%、性能稼働率が95%、良品率が93%の場合、設備総合効率は80% × 95% × 92% = 70%となります。
これは、計画された稼働時間のうち、実際に儲けに貢献できた時間が約7割であることを意味します。数値が思っていたよりは小さいと感じることが多いです。
工場全体の働きぶりとしてこれは良いのか?悪いのか?
設備総合効率の数値を単独で眺めてもわかりませんが、人時生産性や売上高、利益に照らし合わせれば見えてくるものがあります。
ミクロの視点では見逃しがちな問題点も、マクロの視点で初めて明らかになるのです。
設備総合効率は、現場に馴染みのある「出来高」や「時間」といった尺度で評価されるため、工場の現場スタッフにも理解しやすいものです。これを用いることで、製造現場と経営の視点を統合し、チーム全体の結束を高めることができます。
さらに、設備総合効率は金額表示の指標とも組み合わせることで、現場が「出来高」や「時間」から「金額」へのつながりを理解しやすくし、全体の生産性向上に貢献します。
たとえば、人時生産性のような金額表示の指標と共に設備総合効率を掲げることで、現場のスタッフが金額面での目標も意識しながら、日々の業務に取り組むことが可能になります。
これにより、製販一体となって、工場全体の効率向上を目指すことができるのです。
ミクロの視点での詳細なチェックを行いつつ、マクロの視点で全体のパフォーマンスを評価することで、より実効性のある改善活動を推進できます。
その具体的なやり方を指導しているのが実践会です。知識と実務との掛け算で右腕役と現場キーパーソンのポテンシャルを挙げてもらいます。
次は貴社が挑戦する番です!
成長する現場は、働きぶりを出来高と時間でも評価しながら人時生産性を高めている
衰退する現場は、人時生産性を目標としているが金額表示で実感が湧かずお題目で終わる