「生産性ロードマップ戦略」—儲かる工場経営を目指して—第426話 余力がある作業者に何を指示しているか?
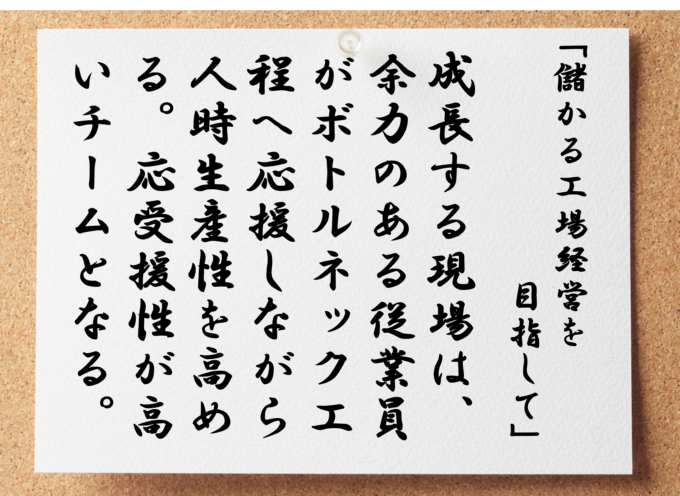
「手が空いたら他の職場の応援をしていました。」
樹脂製品メーカー現場キーパーソンの言葉です。
人時生産性向上の実践会を始めて3ヶ月が経過しました。 計画を立てるには、現状認識(ビフォー)と目標設定(アフター)の両方が必要です。アフターだけは計画になりません。
そこで、プロジェクト計画立案のために、現状把握を並行してやってきました。チームは工場長を含む5名です。まず工程フロー図の作成です。各工程の流れを把握しながら、工程群に分類してから能力を計算しました。
その結果をもとに、メンバーに工程群ごとの能力を明確にすること、そして適正な人員構成を行う目的を説明しました。
その時、メンバーのひとりである現場キーパーソンが前職での経験を話してくれました。冒頭の言葉です。
工程フロー図は、現場の共通言語を湧き出させる「魔法の図」です。
人時生産性向上活動では現状を変えます。現状が現状のままだったから、これまで成果が出なかったのです。それを変えない限り成果は出ません。
活動の最初の一歩は、現状を正しく認識することです。そうでないとビフォーを設定できません。メンバー全員が同じ現状認識を持ち、そこから改善策を導くことが重要です。
現状認識がバラバラだと、会議の場は改革遂行ではなく、現状認識に時間を割かれます。もったいないのです。工程フロー図の造り込みもプロジェクトの成否にかかわります。
工程フローで認識を一致させられたら、具体業務がグングン進むのです。先の現場では人員配置の検証から始めました。やることは能力評価です。
工程フロー図にしたがって、モノ流し方を確認します。
・団子(ロット)で流すのか?
・細切れロットで流すのか?
・1個流しなのか?
工程を分類するわけです。そうして、分類された工程群で能力を評価します。
能力評価は2つです。マシンアワーとレイバーアワー。どちらで評価するかは、現場の主役で決まります。設備が主役ならマシンアワー、人が主役ならレイバーアワー。
そして、能力評価の後に負荷計算です。いわゆる余力管理の能力VS負荷をやります。負荷の計算で作業者の仕事ぶりを明らかにするのです。余力が見えてきます。
多品種少量生産は機能別レイアウトです。効率よりも柔軟性が求められます。そして、柔軟性の裏側にあるのが「一定水準のムダ容認」です。ムダがあるから柔軟性高く対応できます。
効率を追い求めた製品別一貫ラインで柔軟性を求めたら全く機能しません。このことからもムダ容認が柔軟性の背景にあることがわかります。
機能別レイアウトでは各工程の柔軟性の多くは「作業者」によって生み出されています。柔軟性を生み出すために、経営者は作業者に一定水準のムダを容認しているのです。
ただ、それが一定水準ではなく、「作業者」が勝手に決めた水準で、ムダなことをしているなら正さなければなりません。
以前、ご支援していた大型部品切削加工企業の経営者が作業者の仕事ぶりについて語っていました。
「切削加工機が自動運転している間、腕を組んで、設備の前にじっと立っている作業者がいる。」
そのあいだに、もっとやることがあるだろうとその経営者は感じていたのです。的を射ています。1人当たり人件費と1台当たり設備を比較すれば、機械と人、どちらに多くの投資をしているのか、経営者は痛いほど知っています。
コストの安い設備をしゃぶりつくすように稼働させる一方で、コストの高い人が腕を組んでじっと立っているだけでは、固定費回収も覚束無いです。
ただ、設備稼働中の異常音の早期検出のために耳をそばだてて重大故障を未然に防いでいる、だから設備の前にじっと立っているのだ、という作業者の言い分があるかもしれません。柔軟性のためです。
ここから先は経営者が考えるコスパ評価となります。
だから、認めるムダは一定水準なのです。この「ムダ」がどの範囲まで認められるかは、現場が任意に決めるのではありません。経営者が全体のコストや効率性を考慮し、どの程度の柔軟性が必要なのかを決めて、トップダウンで仕事のやり方を指導するのです。
能力VS負荷で評価するのは作業者の余力です。
余力があったら、どうするか?
その工程の出来高を増やすことが工場全体の生産能力を高めるのに貢献するなら、そう指導します。
そうでなければ、その従業員にお願いすることはボトルネック工程の支援です。
「ボトルネック工程への応援で協力をお願いしたい。」
工場全体の能力はボトルネックで全てが決まります。したがって、製販一体でボトルネックを止めないようにするのです。したがって、余力がある作業者がボトルネック工程の支援に回れば工場全体の能力が安定します。
工程群毎に能力を評価す目的は、作業者の余力を明らかにすることにあります。
そして、余力があったら、その作業者にボトルネック工程への応援をお願いするのです。相互補完性や応受援性の高い現場はこうしたことを普通に、自然に、やります。多能工化の指導が必要であることは言うまでもありません。
そもそも中小製造現場は少数精鋭です。少人数で成果を最大化させます。そうであるなら、多能工化を推進し、誰でもどの工程でもできる体制にすることが大事です。
そうやって、柔軟性を維持しながらも人時生産性を高めます。特定の工程しかできないベテラン従業員ばかりでは、高い柔軟性を発揮できません。
チーム力はこうした相互補完性や応受援性の高い現場で醸成されるものです。経営者がそう指導し、導きます。
冒頭の言葉はプロジェクトメンバーのひとりである現場キーパーソンのものです。
前職は自動車部品メーカーで働いていました。大手自動車メーカーの工場がその現場キーパーソンの地元にあります。そうした立地なので、自動車業界で商売をする企業がたくさんあったのです。
そうした企業の現場では、手があいたら、忙しい工程へ回って応援するのが普通でした。冒頭の言葉どおりです。
工場長は、その現場キーパーソンの経験を初めて知りましました。そんないい経験があるなら、どうして今まで、そうしようと言わなかったのだろうか?との疑問が浮かびます。
そのことを現場キーパーソンへ尋ねたところ、次の言葉が返ってきました。
「そうしたことを提案してもやれそうな雰囲気ではなかったからです。」
工場長は、何かに気付いたようです。
次は貴社の番です!
成長する現場は、余力のある従業員がボトルネック工程へ応援しながら人時生産性を高める
衰退する現場は、余力のある従業員に余力があっても自分の工程での作業だけをやっている