「生産性ロードマップ戦略」—儲かる工場経営を目指して—第437話 不良品への対応がモグラ叩き式になっていないか?
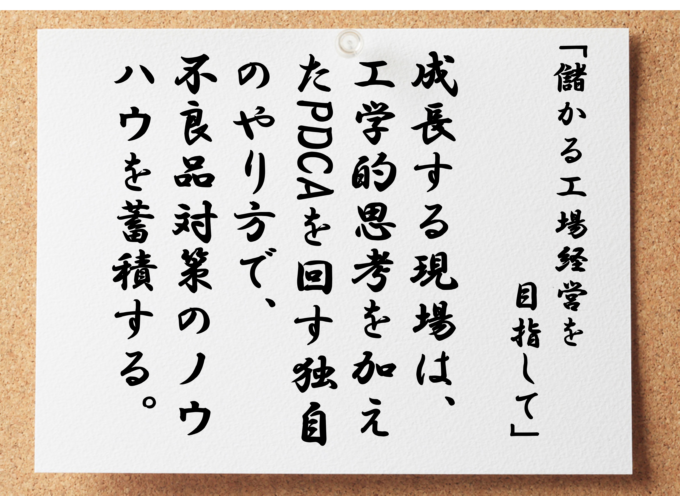
「違いが見つかりました。」
プロジェクトメンバーの現場キーパーソンが、品質不具合品対策の調査結果を説明してくれました。
この企業の経営者は、まさに今、現場改革が必要だと考えています。水面上へ浮上するためです。待ったなしの取り組みに着手しました。
従業員全員が現状を理解した上で、製販一体でベクトルを揃え、社長が決めてきた新規受注品を全てこなせる体制をつくりたいのです。低い人時生産性が問題です。
工程管理の強化をプロジェクトの柱とします。
そのことを、プロジェクトメンバーへ伝えました。
すると、「品質管理の強化も必要だ」との言葉が上がってきました。
現場のコア技術は、金型を使った製造プロセスです。品質が安定しない問題にも直面しています。日々の出来高を増やすには、不良品への対応も必要なのです。
意欲的なメンバーなので、工程管理と品質管理の2本柱になることを厭いません。2本柱でやりたいとの前向きの姿勢を示してくれています。品質管理も加えての、工程管理強化プロジェクトです。
不良品への対応には手順があります。
メンバーは冒頭の成果を報告してくれました。
中小製造企業は分子を積み上げて、人時生産性を高めます。大手のようにリストラはやりません。分母を縮小してしまっては、事業そのものが成り立たなくなるからです。規模の経済で戦う大手とは違った原則があります。
今の人と設備でどこまで出来高を増やせるか?
これが最初の課題です。つまり、工程管理の工数計画です。「能力」VS「負荷」。「能力」をどこまで伸ばせるのか?
「能力」にはマシンアワーとレイバーアワーがあります。仕事量を出来高ではなく、時間で評価するときの考え方です。
マシンアワーの計算項目のひとつに稼働率があります。具体的には設備総合効率です。設備の持ち時間のうち、お客様に届ける商品や製品をつくるのに貢献した時間の割合を示します。
この設備総合効率の構成項目のひとつが良品率です。「能力」を評価するときはリードタイムや不稼働時間だけでなく、良品率も考慮します。
つまり、良品率や不良品率が「能力」に影響を及ぼすのです。製造プロセスによっては、無視できない程度の影響があります。
金型を使用する製造プロセスのなかで、原材料の状態を変化させて素材を製造するプロセスは、良品率や不良品率が能力に影響を及ぼすことが多いです。
樹脂の射出成型では溶融樹脂を固体樹脂に成型します。
アルミ合金の鋳造加工では溶融金属を固体金属に成型します。
ゴム成型では原材料を加硫させて固体ゴムに成型します。
いわゆる、相変態や化学反応を伴う加工は、切削加工や塑性加工と比べて、品質管理項目が多くなります。こうした製造プロセスの作業標準書を見れば一目瞭然です。
温度や圧力、流量、時間など、多数の管理項目がずらぁ~っと並んでいます。
この製造プロセスの使い手は総合格闘技や近代五種競技のアスリートです。多様な手を繰り出さなければ勝てません。油断していると、不良品にやられます。
先の現場はこの総合格闘技や近代五種競技に当たる製造プロセスです。
不良品の発生度合いで日程計画が意図せずに変更されます。不良品が多発すると所定の数量が出来上がるまで、日程が後ろ倒しになるのです。
その結果、日程計画のマスターデータは安全率を高めて設定されます。当然、出来高は積み上がりにくくなるのです。ここに、品質管理も加えた工程管理強化プロジェクトにならざるを得ない背景があります。
品質管理の主な取り組みは2つです。
・品質を数値化する
・不良品が発生する原因を突き止めて、対策を打つ
品質を数値化していないと、対策のbeforeとafterがはっきりしません。「手を打ったけども、それは効果があったのか?なかったのか?」
この判断はノウハウを積み上げるために大事です。
そして、具体活動の柱は「不良品が発生する原因を突き止めて、対策を打つ」です。ここのPDCAを回すやり方を知らなければなりません。
闇雲にやってもダメです。方針があります。
・モグラ叩き式ではなく蓄積式でやる。
経営者は、メンバーへ、そのことを指導する必要があります。
現場は目前の出来事に意識が向きがちだからです。いきおい出てきたモグラを見つけたら、それをハンマーで叩く対応になります。そして、叩き終えたら、そこで安心してしまうのです。そして、再びモグラが出てきたら、ハンマーを持ち出して・・・。この繰り返しです。
ノウハウはチームに蓄積されません。担当者の頭の中に、それまでやってきたことがなんとなく残っているだけです。したがって、担当者が変われば、新しい担当者のモグラ叩きが始まります。
大手と中小の現場での違いについて、経験したことをしばしばお伝えしていますが、中小の現場ではモグラ叩き式が多いです。少数精鋭なので、品質不具合を始めとした、いわゆる「異常事態」への対応がやっつけ仕事にやるのはしかたがないかもしれません。
しかし、この「異常事態」にこそ、我が社の弱点が示されているのです。そこから学びノウハウとします。過去トラによるノウハウの蓄積が大事です。
経営者は、右腕役や現場キーパーソンを蓄積式へ導く必要があります。そして、「不良品が発生する原因を突き止めて、対策を打つ」PDCAを回すやり方を指導するのです。
PDCAを回すにあたって、品質不具合が発生する背景を整理します。
・ルールに関すること
・工学的要因に関すること
前者はさらに、ルールを守っていなかった、ルールがなかった、どちらかに分類されます。なぜなぜ分析で整理できる原因です。
一方、なぜなぜ分析では突き止められない原因もあります。現象の因果関係を把握できていない品質不具合の原因がそうです。
金型を使用する製造プロセスでは、後者の場合があることに留意します。
経営者は、現場が手探り状態になっていないかを判断しなければなりません。先のメンバーはその状態に陥っていました。手順を教えなければならないのです。
工学的アプローチの基本は比べることにあります。したがって、品質OK品と品質NGを比べて、両者の違いを探ることからです。違いのネタをどこまで出せるか?ここがノウハウのひとつになります。
違いが見つかったら、その後はその違いの項目と工学的要因との因果関係を見つけ出すのです。ここでは、ベテランの知見が活きてきます。ベテランの知見を数値化、言語化して、工学的要因を引き出すのです。
製造業は科学であり、工学です。コア技術の工学的要因は理解しておかなければなりません。勘、コツ、経験に工学的思考を加えます。
こうして、「不良品が発生する原因を突き止めて、対策を打つこと」を実践するPDCAを回すのです。その結果、我が社独自のノウハウが蓄積されます。
地道な取り組みです。闇雲にモグラ叩き式を続けてもノウハウが積み上がらないことに、経営者は留意しなければなりません。
違いを見つけた先のメンバーはその差に注目して、次のステップに移っています。工学的要因はベテランの知見を数値化、言語化して整理しました。ある要因に気付いたメンバーがいます。「ここを調べたらいいかもしれません。」こうやって、考えるネタが増えていくのです。
次は貴社が挑戦する番です!
成長する現場は、工学的思考を加えたPDCAを回す独自のやり方でノウハウを蓄積する
衰退する現場は、闇雲にモグラ叩きを続けるだけなのでノウハウが積み上がらず疲弊する