「生産性ロードマップ戦略」—儲かる工場経営を目指して—第438話 仕事に向き合う姿勢をメンバーへ指導しているか?
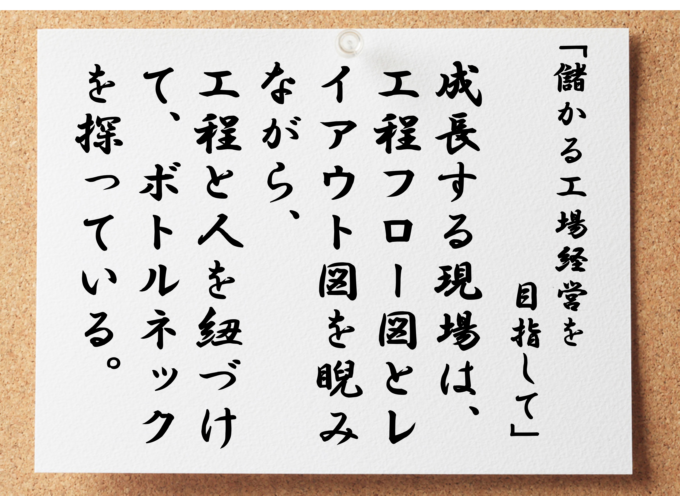
「先生、動線は、どれくらい正確に、書けばいいでしょうか?」
プロジェクトリーダーを担っている工場長が不明点を尋ねてくれました。
切削加工をコア技術としている50人規模部品メーカーです。売上構成は特注品と規格品、半々となっています。人時生産性を高める取り組みを始めたばかりです。
こうした現場では、始めに、規格品で手離れ良く造るやり方を考えます。@付加価値額は小さいですが、一定規模の数量があるので、固定費回収の貢献度が意外と高いからです。工程フロー図を整理した後に、あるものを見極めるためにレイアウト図ともにらめっこをします。
レイアウト図にモノの流れを表現した動線を描くとき、工場長から質問がありました。冒頭の言葉です。
工程フロー図とレイアウト図の両方をにらめっこするのはあるものを見極めるためです。貴社では見極めていますか?
人時生産性向上の要点は分子の積み上げです。
中小製造企業の経営者は市場に身を置いて、新たな仕事を獲りにいきます。電話がかかってくるのを黙って待っているだけでは、ジリ貧です。付加価値額の源泉は全て外にあります。
一方で、現場にもやるべきことがあります。従来の工数のまま、新たな仕事を獲り込めるようにすることです。詰めて、空けて、経営者からの指示を待ちます。
両者が車の両輪のように同期すれば人時生産性は高まるのです。
経営者が外で意志や意図を持って獲ってきた仕事を取り込むのは、現場の仕事です。そのために、詰めて、空けて、待ちます。
右腕役や現場キーパーソンは経営者に代わって、現場で仕事をするのです。
当然のことですが、工場や現場のことが気にならない製造経営者はいません。
だからと言って、経営者が自ら、先頭に立って、ハンマーを振り上げるわけにはいきません。外の仕事に割く時間が減ります。時間が減るとどうなるか・・・。
内の仕事を全て右腕役や現場キーパーソンに任せる体制がなければ、事業を成長させられないとお伝えしている所以です。
「詰めて、空けて」とは、すなわち、リードタイム短縮のことです。細かく繋ぎ、サクサク切り替え、手離れ良く造ります。
そうすれば、ロット毎リードタイムが短縮され、さらには工場平均リードタイムが短縮されるのです。仕掛品を増やさずに付加価値額を積み上げられます。
経営者は運転資金を増やさずに事業を成長させる要点を忘れてはなりません。
現場での取り組みが工場経営にも直結することを右腕役や現場キーパーソンへ教えるのは経営者の仕事です。
現場では、細かく繋ぎ、サクサク切り替え、手離れ良く造りたいのです。そして、これはモノの流れで決まることです。
そこで、右腕役や現場キーパーソンがやらなければならないことがあります。工程フロー図の作成です。モノの流れをこれで記述します。工程設計です。
部品は単線、組立品は複線で表現され、工程と工程間の数がわかります。
例えば、工程と工程の間には、「運搬」「停滞」「運搬」の工程が自然発生的に生まれる原則は憶えておきたいです。「運搬」「停滞」は価値を生みません。
工程フロー図の目的は、工場全体のモノの流れを見えるようにすることです。プロジェクトメンバー同士の効率的な議論を後押ししてくれます。
メンバー全員がモノの流れについて、同じ情報を持っていたら、無駄な時間を省けます。モノの流れ、今、どうだったっけ?」と言っては、現状の確認に時間を割かれるような事態をなくせるのです。
「詰めて、空ける」ためには、メンバー全員が、今のモノの流れを把握している必要があります。工程フロー図はメンバーのベクトルを揃える魔法の図です。
ただ、工程フロー図で注意しなければならないことがあります。それは、工程フロー図は必ずしも現場の状況を正確に描写しているわけではないということです。
ある意味、現場でのモノの流れを抽象化しています。「工程」という単位で抽象化したものです。抽象化しているから、思考が整理しやすくなっています。
そして、工程は、さらに、「作業」という単位で抽象化されているのです。こうやって、工程フロー図は、考える手がかりを与えてくれます。
しかし、現場の実態を生々しく表しているわけではありません。
そこで、工程フロー図をレイアウト図へ書き込む作業が必要になります。
書き込むのは、動線、工程および作業のエリア、人員配置です。レイアウト図に工程フロー図を書き込むと、抽象的だった工程フロー図が具体化されます。
具体-抽象-具体は分析に必要な思考です。
レイアウト図に工程フロー図を書きこむ目的はボトルネックの見極めです。規格品生産の生産性向上では特に欠かせない論点となります。
ボトルネックを見極めるために動線、工程および作業のエリア、人員配置を書き込むのです。したがって、冒頭にあった動線の正確さは、ボトルネック見極めができれば、それでOKとなります。
モノの流れを見えるようにするだけなので、動線の正確さは必要以上にはいりません。
そして、レイアウト図に書き込まれた動線、工程および作業のエリア、人員配置から「工程および作業」と「人および設備」を紐づけます。ここが要点となります。
これで、抽象的な工程フロー図が具体的になり、ボトルネックの要因となる人および設備が特定されるのです。
中小製造現場では大手とは異なり、人がボトルネックになることがあります。これこそが柔軟性の源泉でもあるのですが、属人的が故に、長期的には解決しなければならない問題です。
こうやって、ボトルネックになる人および設備を特定したら、そこに投入できる工数を評価します。そして、これが我が社の生産能力となるのです。
これをもとに工数計画を立てます。
人時生産性向上のようなプロジェクトに取り組む際、その仕事に向き合う姿勢は大事です。
業務には目的があります。目的を理解して業務をするよう、右腕役や指導するのは経営者の仕事です。
ここが欠けている従業員は自ら考えることもなく、作業をこなすだけになります。言われたとおりにやるだけです。これは自責ではなく、他責の姿勢に繋がっています。
経営者は、このような右腕役や現場キーパーソンに、工場のことを、任せることはできません。問題が出る度に、できない理由ばかり言うメンバーに付き合っている暇はないのです。いきおい、経営者は外の仕事に専念できなくなります。
冒頭の「動線はどこまで正確に書けばいいでしょうか?」は、業務には目的があるということを理解しているから出てくる質問です。課題に対する反応や感度の高い、チームです。
こうした質問をドンドン出してくれる右腕役や現場キーパーソンなら、経営者は工場のことをメンバーへ任せられます。
ノウハウの習得の前に大事なことがあるのす。
貴社はどうでしょうか?
全ては経営者によるメンバーへの訓練次第です。
「なるほど、多能工化を進めなければならないわけですね。」
工程フロー図をレイアウト図へ書き込む作業を終えて、ボトルネックを見極めた後の工場長が語ってくれました。この現場でも人がボトルネックになっています。
それを解消するための多能工化です。全ての仕事には目的があることをしっかり理解している工場長です。
次は貴社の番です!!
成長する現場は、工程フローとレイアウトを観ながら工程と人を紐づけボトルネックを探る
衰退する現場は、工程フローやレイアウトを見える化していないからそもそも議論できない