「生産性ロードマップ戦略」—儲かる工場経営を目指して—第451話 遅れに対する感度を高めているか?
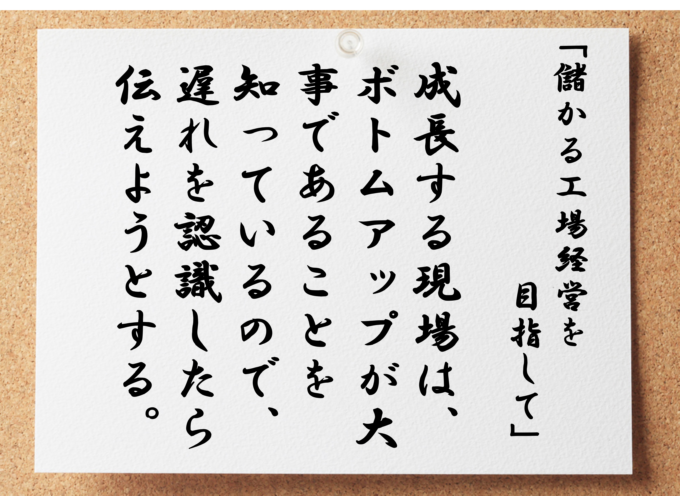
「完了だけでなく、”着手”もフォローしないとだめです。」
人時生産性向上プロジェクトが、佳境に入ってきた部品メーカー工場長の言葉です。
人時生産性を高める具体策は複数あります。山登りで登山ルートが複数あるのと同じです。プロセスが異なっても、全てのルートは山頂を目指します。製品特性や仕事のやり方を踏まえて登山ルートを選ぶのです。
プロジェクトリーダーである工場長は「製造ロット毎リードタイム」に焦点を当てる「登山ルート」を選びました。特注品生産に近い多品種生産だからです。
リードタイム構成要因を明らかにしてから、その短縮を考えます。構成要因のbefore/afterを設定して、ギャップを埋めていくのです。
日程計画を使って、現場に「時間や時刻」を意識させます。朝礼で出された作業指示の進捗を作業日報でチェックするのは、リードタイム短縮具体業務のひとつです。進捗確認では、主に、予定通り終わったか、終わっていないかを、確認します。
ただ、それだけでは不十分だと工場長は考えました。
冒頭の言葉です。
●日程計画は仕事量で示される
人時生産性向上のキモは分子の積み上げにあります。経営者であるなら、現在の人員と設備で最大限の積み上げをしたいのです。今ある経営資源をしゃぶりつくします。これが、少数精鋭の中小現場で、生産性を高める初手の考え方です。
生産形態がなんであれ、経営者は、今の生産能力を「金額」ではなく、「仕事量」で把握しておく必要があります。
工場の現状を売上高で説明する経営者は多いです。工場経営上、当然大事です。ただ、現場へ働きかけ、やる気を引き出すには、これだけではできません。現場が認識しているのは金額ではなく仕事量だからです。
日程計画は、仕事量で示されます。ロードマップや経営計画で、我が社の将来を従業員へ示すとき、売上高と共に仕事量の説明が必要である所以です。経営者の意志や意図を、現場へ浸透させるには、理解させて、伝える工夫が欠かせません。
●日程計画があればbefore/afterを設定できる
生産性向上の取り組みにおいて、日程計画は大きな役割を果たしています。種々仕事量のリードタイムが日程計画で示されるのです。
日程計画があれば、リードタイム構成要因のbefore/afterを設定できます。
ある製品が出来上がるのに、従来、10日間掛かっていたとします。
製品の流し方、作業者の仕事ぶりを大幅に見直した結果、トライアルではありますが、6日間でできるようなりました。
そうしたら、次は、現場が、そのやり方を無理なく継続できるかの検証です。日経計画で確認します。6日後にきちんと完了したかどうかのフォローと評価です。製造ロット毎のフォローを継続します。
検証の結果、6日間で完了する製造ロットの割合が8割以上になっていれば、概ね上手くいっていると判断できます。後は経験値を高めて、6日でやるやり方が「普通」になるのを見守るだけです。
●遅れの認識は早ければ早いほどイイ
進捗フォローでは、仕事の「完了」を都度、チェックします。種々仕事量が所定のリードタイムで、予定通り、終わったかを判断するのです。もし終わっていなければ、この時点で「遅れ」を認識することになります。
遅れを認識したら、挽回しなければなりません。そして、挽回策を講じるのは、早ければ早いほどいいわけです。
・リードタイム6日間の製造ロットで、出荷の前日に遅れを認識した。
・リードタイム6日間の製造ロットで、出荷の4日前に遅れを認識した。
前者は後ろから追いかける工程管理、後者は前から追いかける工程管理となります。どちらのやり方が、現場にとって楽であるかはあきらかです。
遅れの認識が、早ければ早いほど、現場は楽に挽回ができます。経営者は、そのことを右腕役や現場キーパーソンへ教える必要があります。バタバタするだけがやり方ではありません。
●遅れへの感度を高める
先の工場長は、「遅れの認識は早ければ早いほどイイ」ということを理解しました。そして、「完了」だけでなく、「着手」もフォローすれば一層効果が上がる、と考えたのです。
さらに、その日の夕方、就業終了時点だけでなく、その日の、昼間、折り返し時点でも、進捗のフォローをすれば、遅れに対する「感度」を高められると考えました。
・「完了」に加えて、「着手」もフォローする
・夕方に加えて、昼間もフォローする
こうやって、遅れへの「感度」を高めるのです。「感度」が高まれば、現場に時間や時刻を意識させることになります。日程計画が強化され、リードタイム短縮を実践する環境が整備されるのです。
●現場から情報を得る
徹底した効率を追い求める大手の製造現場は、自動化、機械化、設備化、無人化され、属人的要因を排除しています。各種のセンシング技術によって、「遅れ」をデータで認識できるようにするのです。
自動車部品工場時代、エンジニアとして担当した工程でもそうでした。「遅れ」有無のほとんどが、リアルタイムで把握されていました。
一方、中小製造現場でのやり方は違います。主要な工程、作業のオペレーションは、人に依存することがほとんどです。
これは、中小製造企業強みを発揮するための体制とも言えるのですが、「遅れ」の認識も人に依存せざるを得なくなっています。現場のことは、現場が一番知っているのです。
仕事の状態を3通りで認識できます。
・まだ「着手」していない。
・「着手」したけれども、「完了」していない。
・「完了」した。
こうした情報を現場から得たいのです。人に依存した中小現場で、多くの情報はボトムアップで獲得されます。4階層指示導線を機能させることも要点です。
●チームのコミュニケーション能力を高める。
進捗フォローは、原則、毎日、継続的にやるものです。
例えば、朝礼は必ず、朝一でやられます。これは、どこの中小製造企業で同じでしょう。習慣化されています。それと同じくらい、進捗フォローを、習慣化して、継続的に、無理なくできるようにしたいのです。
・「完了」に加えて、「着手」もフォローする
・夕方時点に加えて、折り返しの昼時点でもフォローする
上記をやるために、作業日報を改訂するとか、ホワイトボードで状況を見える化するとか、口頭で報告させるとか、やり方はいろいろあります。ただ、もっと大事なのは、迅速なボトムアップができる環境整備です。
・作業者、現場キーパーソン、右腕役、チームのコミュニケーション能力を高める。
迅速で、密な、意思疎通です。進捗フォローの目的は、フォローすること自体にあるわけではありません。目的は「遅れ」の挽回にあります。少しでも早く、「認識」したいのです。
●遅れの報告の重要性を理解させる環境整備も大事である
ボトムアップが大事である、遅れを認識したら教えて欲しい、遅れ自体を責めることはしない、遅れを教えてくれないことは責める、などと、日頃から指導していれば、現場の作業者は上司へ伝えようとします。躾です。
ボトムアップの仕組みづくりに加えて、ボトムアップの環境整備が大事です。これは経営者にしかできない仕事です。
作業者が「遅れを報告することは大事である」ということを、繰り返し聞かされていれば、なんとか伝えようとします。ボトムアップはトップダウンとセットであり、躾できちんと指導していくものです。
製販一体、全社一体、チーム力が高い組織は、ボトムアップがしっかりできています。遅れへの感度が高く、進捗フォローの重要性を理解できているのです。
次は貴社が挑戦する番です。
成長する現場は、ボトムアップの重要性を知っているので遅れを認識したら伝えようとする
衰退する現場は、ボトムアップの重要性を知らないので、遅れてもそのまま作業をしている