「生産性ロードマップ戦略」—儲かる工場経営を目指して—第80話 受注できるかどうかを日程計画で明らかにする
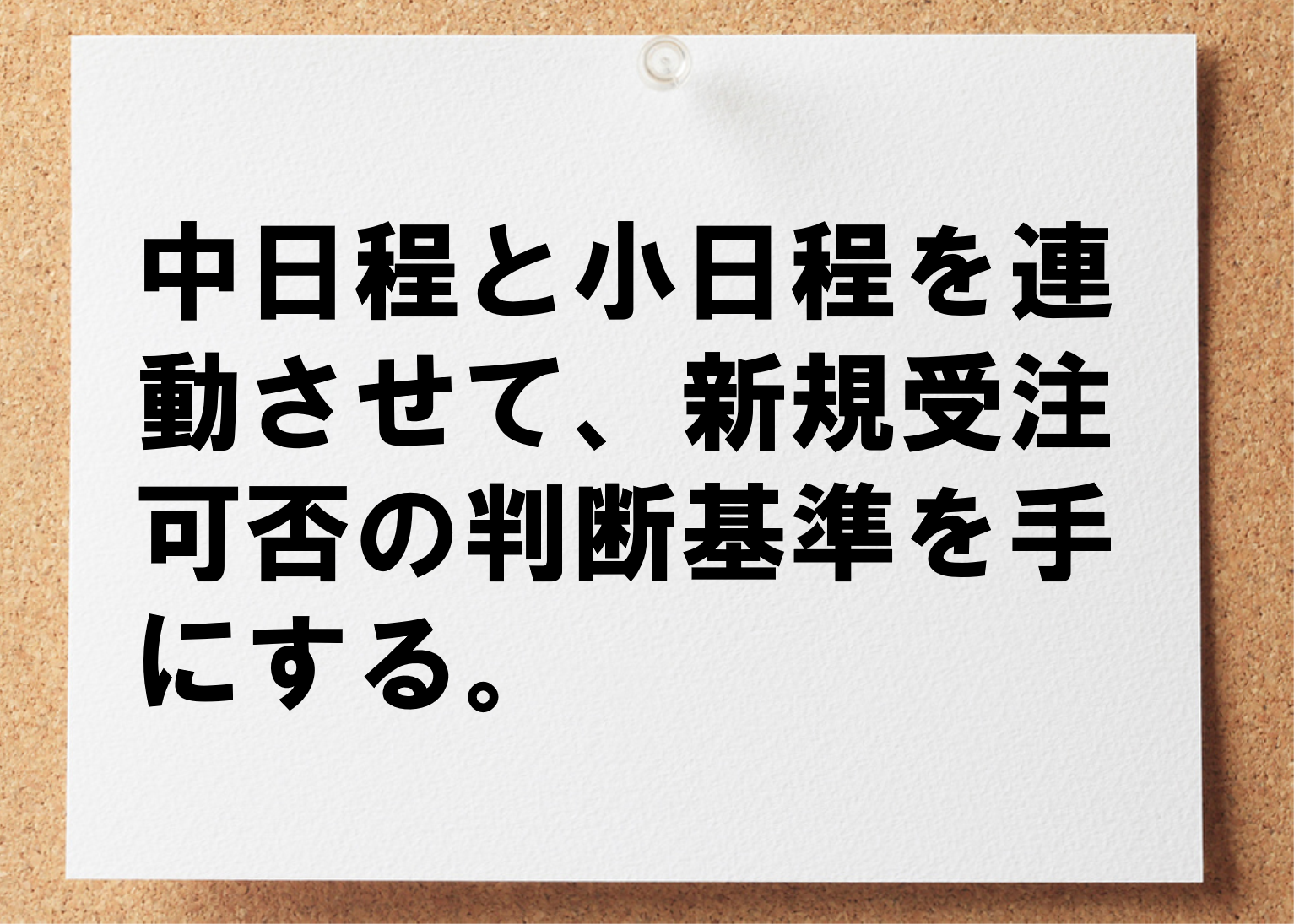
貴社では新規受注案件の納期を明確に提示できますか?
「1~2か月先の生産計画が立てられなくて、新規受注の機会を逃しています。
どのように立てたらいいでしょうか?」
最近、このような経営者の声を耳にすることが増えてきました。
先週も、異なる業種(金属加工と金属製品製造)の経営者から、同じようなご相談を受けました。
現場の自発的な柔軟性だけで、多様な受注案件へ対応する従来の仕事のやり方は、もう限界のようです。
モノづくりは高度化、複雑化する上に、多品種少量化、短納期化というのが”普通”になってきました。
工程管理は生産計画と生産統制で構成されていますが、前者の重要性が、確実に高まってきています。
現場と経営者の勘と経験だけで、現場の状況を把握し、受注の可否を判断するには、状況があまりに複雑になりすぎており、生産計画を組織で活用する仕事のやり方が求められているのです。
新規受注を受けるにも、突発案件へ対応するにも、余力の判断基準がなければ、経営者は意思決定ができません。
したがって、現場の余力を見える化するため、現場は精度の高い生産計画を立てられるようになる必要があります。
先にご相談をいただいた経営者の現場もそうですが、客先で組み立てる製品の部品加工を事業の柱に据えている中小製造企業も多いです。
地域に密着し、高い設計力や加工技術力を強みに顧客へ価値を提供しています。
そうした現場の生産形態は、押し出し方式です。
部品製作に必要な原材料を手配し、揃えるところからスタートします。
そして、複数の工程を通過させて、その原材料に加工を加え、部品に仕上げるのです。
手順計画で工程を設計しますが、部品ごとに工程が異なるので、生産現場では、流動する部品の加工の進み具合を逐一、把握することが必要があります。
そこで、欠かせないのが、日程計画です。
”加工の進み具合を逐一、把握する”とは、進捗管理のことであり、押し出し方式における進捗管理のキモは「過程管理」となります。
進捗管理には2通りあります。
・「数量管理」
・「過程管理」
大ロットで同じ仕様の製品を製造する現場では、出来上がり製品の数量を追っかけなければなりません。
計画対比で数量の遅れを認識したら、残業、外注などで挽回します。
これが数量管理です。
流動数曲線で見える化すると効果的です。
一方、多くの部品加工現場で必要とされるのは過程管理です。
こちらはガントチャートで見える化できます。
ガントチャートを活用し、所定の工程が、所定の日時に完了いるか否か確認するのです。
管理者は設定した納期を遵守できるよう、事前の計画と現状を比較します。
そして、事前の計画として、日程計画が必要となるのです。
全ては、この日程計画次第であり、日程計画の精度で勝負がつきます。
貴社では、2~3か月後の日程計画および1週間の日程計画を、どの程度の精度で設定できるでしょうか?
半月単位、週単位、日単位、半日単位、時間単位。
時間単位が小さければ小さいほど、精度が高まります。
さて、日程計画は3本柱です。
大日程計画、中日程計画、小日程計画。
これらの具体的な活用方法は、セミナーやご支援時に説明していますが、押し出し式の生産形態では、それぞれ、次のような、明確な目的があります。
大日程は利益の見える化。
中日程は余力の見える化。
小日程は柔軟性の見える化。
先にご相談があった企業に必要なのは、大日程もさることながら、特に中日程と小日程の連動でした。
今後は、現場の柔軟性を高めるため、小日程と中日程を連動させることがキモとなります。
そして、生産計画の体系で日程計画の精度を高めるのです。
時間軸をどんどん細かくしていきます。
従来のモノづくりなら、小日程計画のみを使い、直近の納期を遵守することに全力を挙げていれば、概ね問題はありませんでした。
しかし、中小製造企業の外部環境はどんどん変化しています。
高度化、複雑化、多品種少量化、短納期化。
息をつく暇もないほどです。
そうした変化を受け、仕事のやり方も変えていかなければなりません。
部品加工を事業の柱としている押し出し方式の生産形態の現場で、今後必要なのは、日程計画、特に中日程と小日程を連動させることです。
「過程管理」を強化して、”今”の状態を、精度高く知る仕組みをつくります。
そこで、中日程で現場の余力を把握し、小日程を現場全員で共有するのです。
あらゆる事態へ柔軟性高く対応できる現場になります。
小日程と中日程を連動させる仕組みをつくることで、経営者は新規受注可否の判断基準を手にするのです。
勘と経験で乗り切っていた仕事のやり方を変えます。
新規受注ができるかどうか、意思決定する仕組みをつくりませんか?