「生産性ロードマップ戦略」—儲かる工場経営を目指して—第96話 リードタイム短縮で間接的な決定権を獲得する
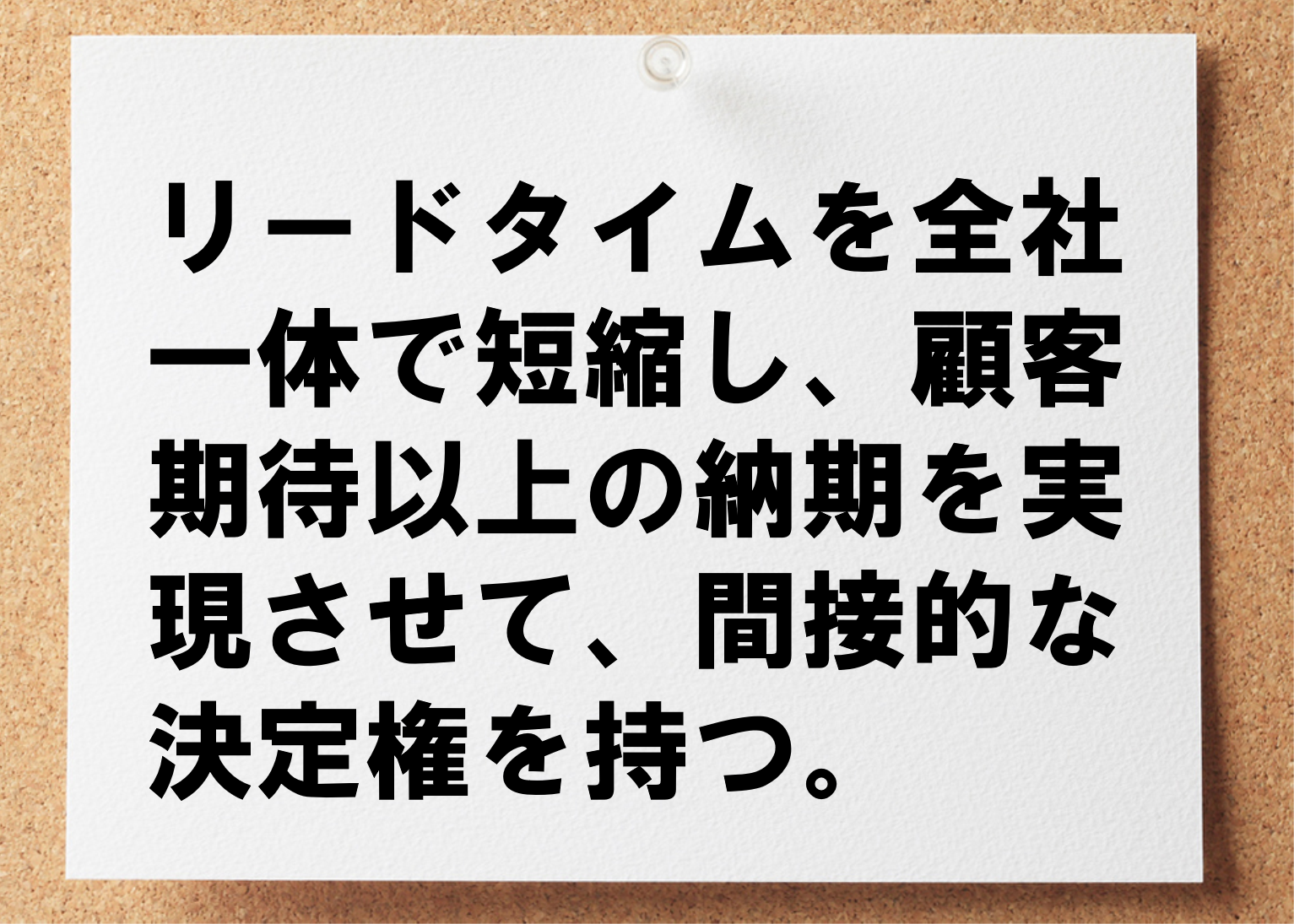
マクロとミクロ、リードタイムの定義を使い分けていますか?
生産3条件とはQCD、つまり品質、コスト、納期のことです。
モノづくりの事業を有利に進めたかったら、これら3条件の決定権を手に入れることです。
・製品の品質、仕様を自ら決められる。
・製品の価格を自ら決められる。
・製品の出荷日を自ら決められる。
理想の姿ではないでしょうか?
生産3条件のうち、1条件でも決定権を持てると有利です。
しかし、事情はそう簡単ではありませんね。
皆さんもご存知のように、原則的には、”顧客”が、生産3条件の決定権を持っています。
これは、自社ブランド品を見込生産している企業であっても同じです。
顧客との対話なしに、売れる商品を市場に出し続け、安定した売上を維持することは難しくなっています。
受注生産形態で下請け型の事業を展開している企業ならなおさらです。
仕様は顧客からの指示、納期も顧客都合優先、加えて価格も顧客からの指し値という場合も少なくありません。
生産3条件の決定権は100%完全に顧客側にあり、顧客に求められるがまま、取引せざるを得ない現場もあるのではないでしょうか?
下請け型の事業を展開している中小製造企業が少なからずありますが、こうした現場では、厳しい納期を遵守しながら頑張っています。
次の仕事へつなげるためです。
しかし、ただひたすらに納期遵守だけの仕事では疲弊します。
そこで、中小製造企業の経営者には、ひと踏ん張りをお願いしたいのです。
生産3条件のひとつに焦点を当てます。
そして、全社あげて、一体感を持ち、計画的、体系的に、その生産条件の決定権を狙うプロジェクトを進めるのです。
それが納期です。
製品仕様や価格で差別化が困難であっても、その納期が”圧倒的”なものであったら、顧客の関心を引くことができるのではないでしょうか?
短納期、超短納期は、現場の競争力を高めるとともに、お金になる可能性があります。
弊社でリードタイムを重視する所以です。
リードタイムの定義にはマクロとミクロ、2つの観点があります。
受注情報が届いてから出荷するまでの各工程所要時間をひとつずつ積み上げるのがミクロの定義です。
受注形態のリードタイムを例にして具体的に説明します。
ミクロの定義では、製品個別の実績を詳細に分析できます。
・注文L/T=作業指示L/T+生産L/T
・生産L/T=正味加工時間+ロットサイズL/T+工程間待ちL/T
受注形態の現場では、作業指示L/Tに設計・開発の時間が含まれます。
一方、現場の在庫状況から評価するのがマクロの定義です。
平均の生産リードタイムを算出するのに在庫と出荷量、平均の注文リードタイムを算出するのに受注残と出荷量に着目します。
・平均の生産L/T=(仕掛品+出荷待ち品)量÷1日当たり出荷量
・平均の注文L/T=受注残÷1日当たり出荷量
上記のように現場全体の平均を評価できます。
リードタイム管理ではミクロとマクロを使い分けたいです。
・どの工程にリードタイム上の問題点があるのか分析したい。
・製品毎のリードタイム短縮を個別具体的にすすめたい。
この場合はリードタイムのミクロ分析です。
ミクロのリードタイムを管理するには、工程管理体制が敷かれ、各工程からリードタイムの実績が上がってくる必要があります。
現場での作業日報や生産実績報告など報告が徹底されていなければ、精度の高いデータになりません。
・工場の実力としてリードタイム実績を把握したい。
・リードタイム実績の推移をざっくりと把握したい。
工場全体、現場全体、生産ライン全体の実力を把握したいときはマクロ分析です。
その推移もしばしば論点となります。
原材料や仕掛品、製品の在庫を管理している現場なら、平均リードタイムはすぐに評価できます。
1日当たりの出荷量で除すればいいわけですから。
リードタイムと仕掛品量はほとんど同義です。
リードタイムを短縮しようとすれば仕掛品が減ります。
また、仕掛品を減らそうとすればリードタイムが減ります。
生産の流れをつくるというのはリードタイムを短縮することであり、仕掛品を減らすことに他なりません。
マクロの定義で工場全体の実力を測ることができます。。
特注生産が事業の柱となっている金属加工現場で、生産リードタイムを話題にしたことがあります。
現場リーダーへ下記のように尋ねました。
「受注してから出荷するまでの平均日数はどれくらいですか?」
製品がいろいろあって全く把握できていません、というのが答えでした。
受注と出荷の管理システムはあるのですが、それは会計処理のために使われています。
これらのデータを生かさない手はありません。
「受注したけれども生産未着手の案件と生産に着手して現場に仕掛っている案件を把握してみましょう。」
リードタイムのマクロの定義です。
まずは、ざっくり現場の実力を評価しました。
「在庫の規模感でリードタイムが分かるようになりますね。」
数字を目にしたその現場リーダーの言葉です。
つまり、仕掛品や完成品の在庫規模(見た目の容量)からリードタイムという時間の長さを理解できるようになります。
1日当たり出荷量を一定とすると、在庫量からリードタイムを読めるのです。
リードタイムは、生産性とともに、モノづくり力を測る重要指標と考えていますが、それは在庫量を評価していることに他なりません。
在庫増減の推移は、リードタイム長短の推移でもあります。
マクロの定義では、平均リードタイムの推移を簡便に評価できるのです。
リードタイムのマクロとミクロの定義を使い分けて、リードタイムへの感度を高めます。
リードタイムを切り口に生産管理3本柱を磨くのです。
顧客期待以上の納期を実現できれば、”間接的”な納期の決定権を獲得できます。
納期への自由度が高まるからです。
多くの経営者に”間接的な”決定権を持っていただきたいと考えています。
下請け型の事業でも、QCDを極めれば主導権を握れるのです。
そうした事業展開を目指したくないですか?
リードタイムをマクロとミクロで把握する仕組みをつくりませんか?